CAE活用に向けた「前さばきの手法」で製品機能の全体像を見える化
支援内容 |
|
---|
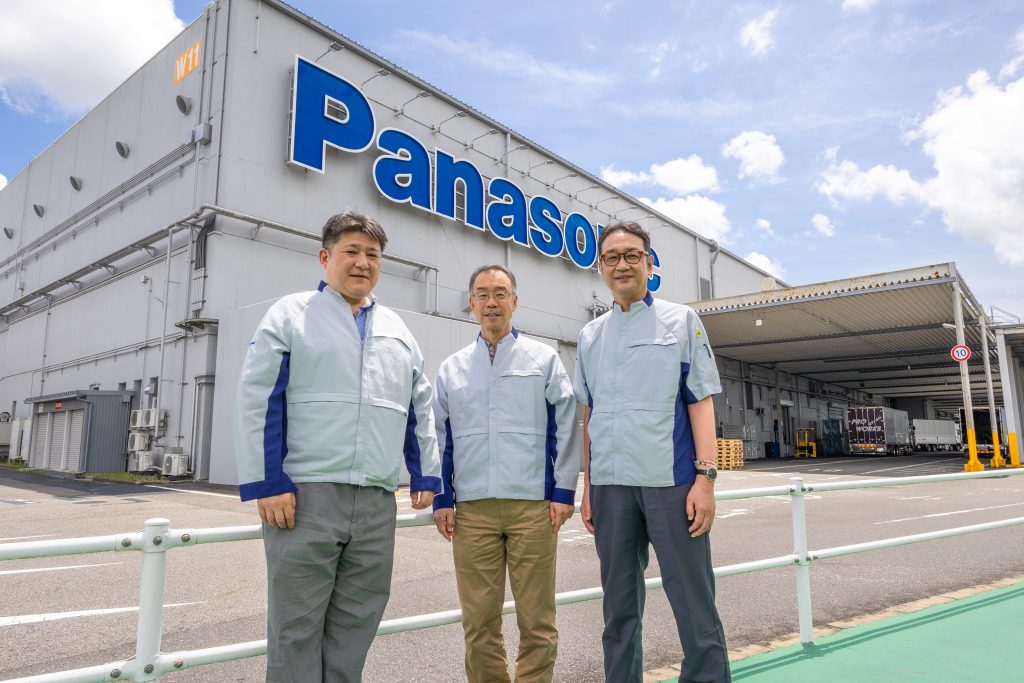
パナソニック株式会社で白物家電事業を担う「くらしアプライアンス社」。その事業体制は、製品の設計生産を行う「事業部門」と、事業枠を超えた横断的な先行技術開発や業務効率化等を推進する「本部」に分かれています。今回、オーツー・パートナーズは、本部からの依頼で、DX戦略(ECMデジタル化)を支援。特に重要課題として位置づけられた「CAEの活用・定着化」の取り組みについて紹介します。
【お客様からのコメント】
※以下、所属および役職については、プロジェクト活動当時(2023年12月末時点)の名称です
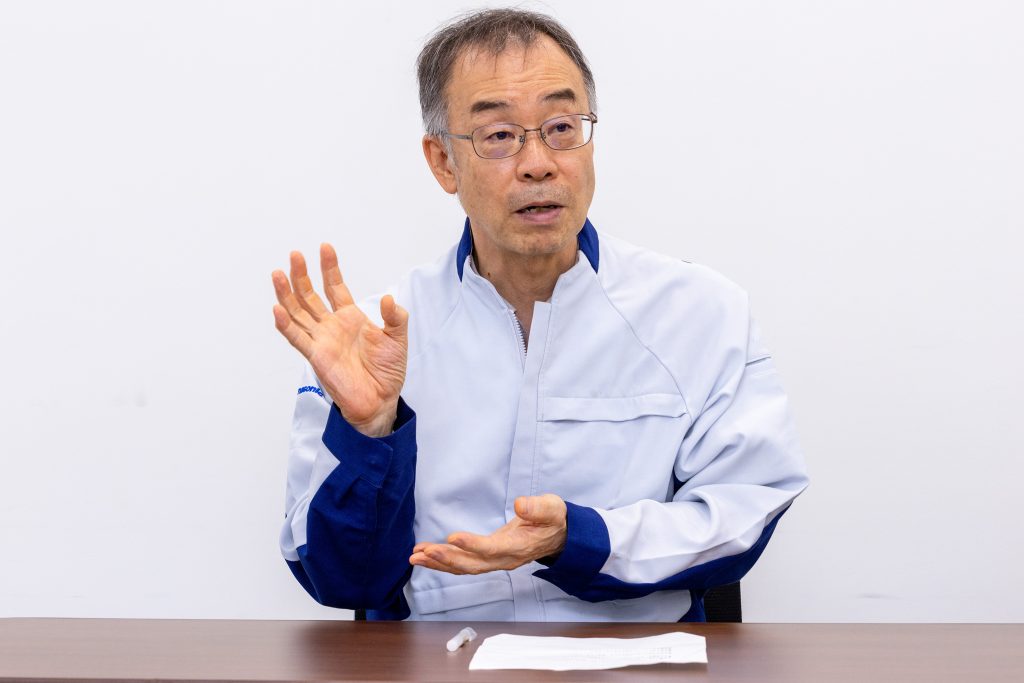
「今回、オーツー・パートナーズの支援を受けたことで、CAEを活用しながらデジタル化へ進むための道筋がはっきり見えるようになりました。さまざまな角度から、熱心に対応していただいたことに、とても感謝しています。 また、論理的な手法や具体的な手順を示していただいたことでメンバー全員が納得。若手エンジニアが積極的に取り組むなど、長年苦戦してきたマインドチェンジにも成功したと思います。」
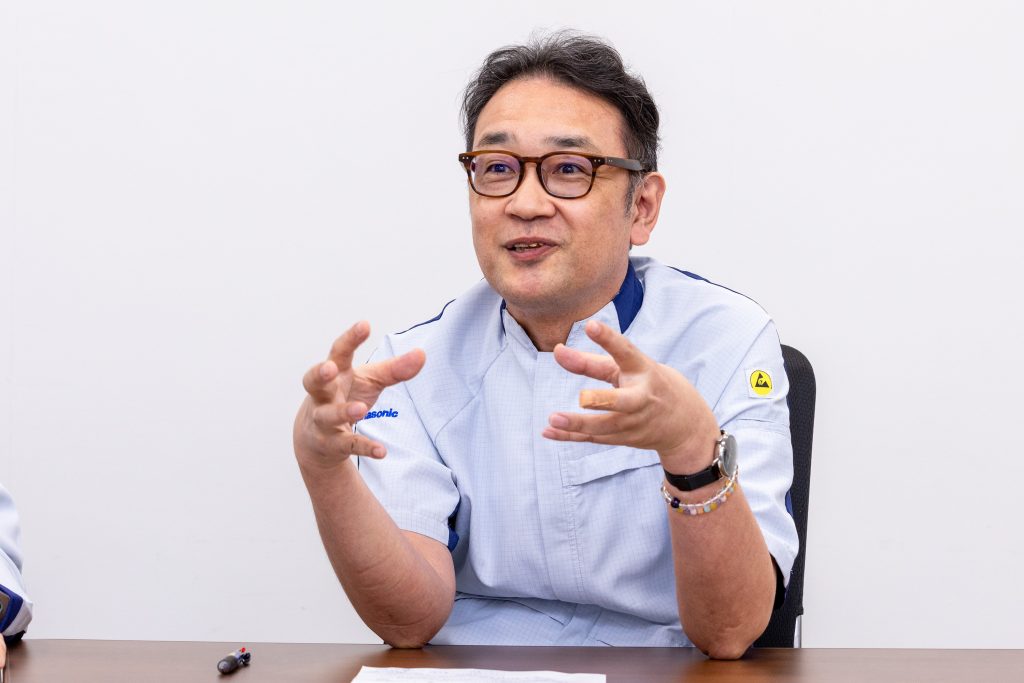
「オーツー・パートナーズからアドバイスを受けつつ『機能設計5点セット』を作成したことで製品全体の機能俯瞰ができ、エンジニアとして仕事の見え方・解像度がガラッと変わりました。自分が担当する範囲を超えた開発要素や機能の繋がりも可視化され、若手もリスクを勘案しながら新機能の開発にチャレンジしやすくなり、上司はそれに対する判断をしやすくなりました。これが当プロジェクトの最も大きな成果だと思います。」
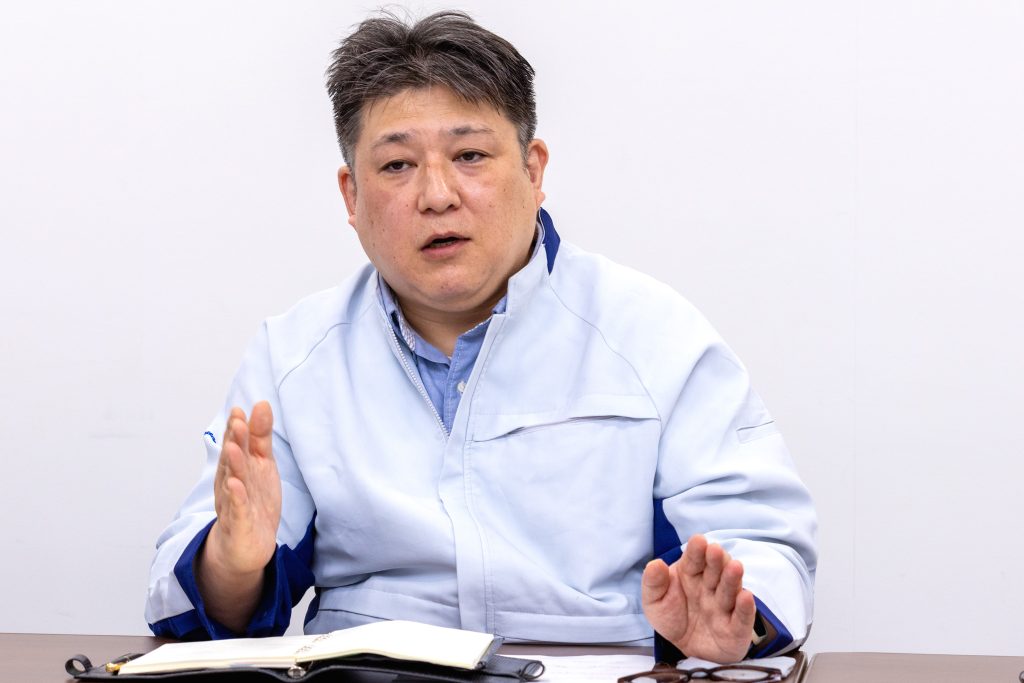
「はじめは“一刻も早くCAEを浸透させたい”という想いでいましたが、プロジェクトを終えた今となってみると、それは小さなことだったと分かります。CAEはあくまで手段の一つ。CAEありきではなく、まずは私たちが設計でめざすゴールを明確にすることが大事なのだと気づかされました。また、事業部門と対話を重ねることで、同じ方向を向けるようになったことも良かったです。」
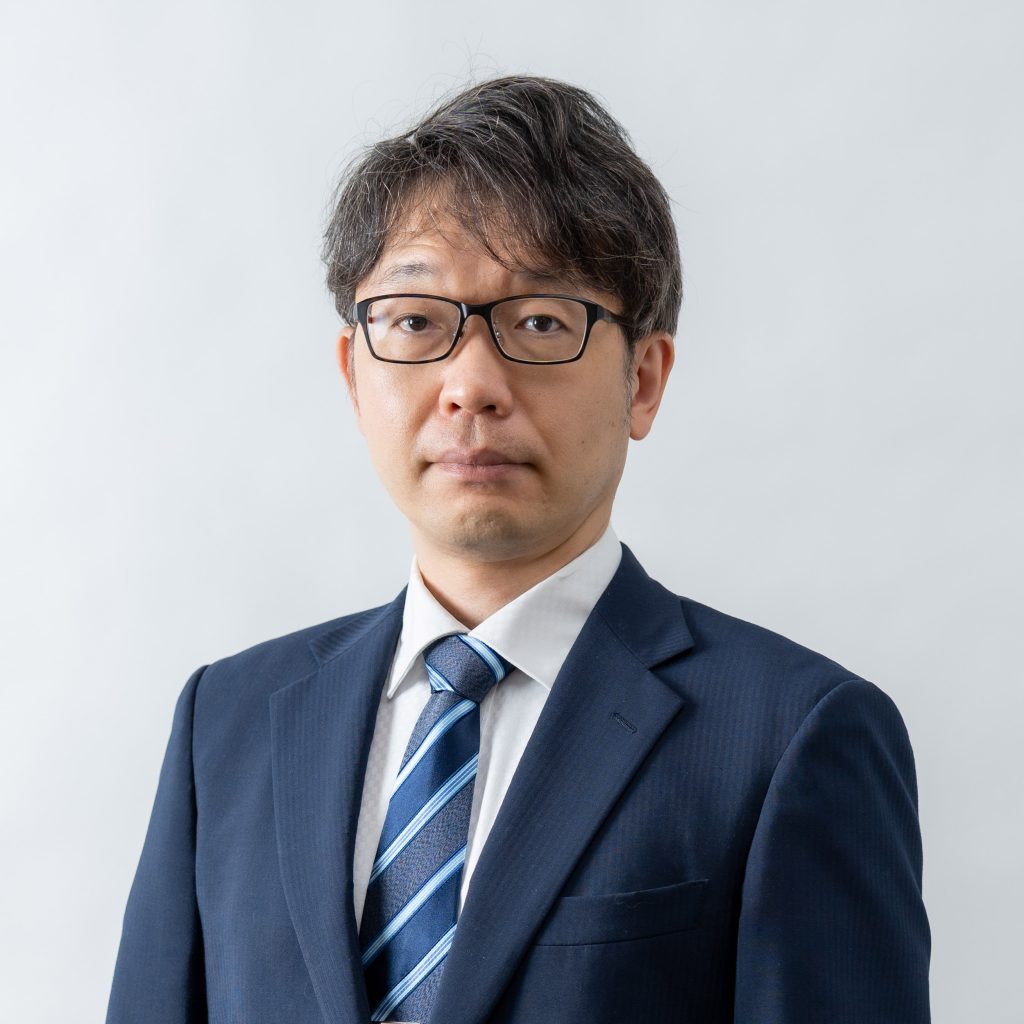
担当プロジェクトマネージャー
長嶺 晋路
国内自動車メーカー出身、製品開発及び生産技術に従事。2020年からオーツー・パートナーズに参画しコンサルタントに転身。MBD含むDX企画構想から設計業務の可視化、自動設計環境の構築と言った企画から自動化までの一連のECM業務改革を得意とする。
【ご支援概要】
- DX戦略(ECMデジタル化)における「CAE活用・定着化」
- CAE活用前の「前さばきの手法」、機能設計5点セットの提案
- ワンチーム化による開発現場のマインドチェンジ
【ご支援先】
パナソニック株式会社 くらしアプライアンス社
パナソニック株式会社 くらしアプライアンス社(以下、くらしアプライアンス社)は、パナソニックグループの中で「食」「家事」「美容・健康」にかかわる白物家電事業を担う社内カンパニーです。これまで、同社が数々のイノベーションを起こし、時代をリードする家電を送り出してきた背景には、事業部門間を横断的につないできた「本部」の存在が欠かせませんでした。現在も、本部を中心にECM(※1)やSCM(※2)の改革、顧客との接点づくりなどに注力し、全社のデジタル化に向けて本格稼働を始めています。松下幸之助氏が旧松下電器産業を立ち上げてから100年以上。パナソニックは進化を止めることなく、私たちの暮らしを支える製品を生み出し続けています。
※1 エンジニアリングチェーンマネジメント。製造業の設計・開発プロセス管理。
※2 サプライチェーンマネジメント。製品の調達から販売までの一連のプロセス管理。
本当の意味での「CAEの活用・定着化」をめざす
くらしアプライアンス社の本部は、「DX・顧客接点革新本部」「くらしプロダクトイノベーション本部」「ビジネスプロセスイノベーション本部」という3つの組織で構成されています。その名称からも分かるように、改革やイノベーションを起こすことがミッション。さまざまな角度からDX改革に取り組む中、早急に取り組むべき課題として挙げられたテーマが「CAEの活用・定着化」でした。
「CAE自体は30年くらい前から導入していたものの、主な使い方は、実機(試作)に不具合が起きたときの検証や、すでにでき上がっている製品の改良など、ある程度設計が進んでからの適用がメイン。本当の意味で“CAEを設計に活かしている”とはいえない状況でした。」(西口氏)
実機(試作)を作り、テストや評価を繰り返しながら、設計を完成させていくというのが、これまでの同社の開発スタイルでした。しかし時間もコストもかかるこのやり方では、少子高齢化による人材不足や、競争力の激化に対応していけないと、本部は危機感を強めていました。
「企画構想や先行開発の段階からCAEを活用できれば、リードタイムの短縮や試作の最小化につなげることができます。しかし、どうすれば上流からCAEを浸透させることができるのか…。道筋が見えない状態でした。」(津田氏)
いわゆる「形のない段階」から、CAEを活用して設計ができる体制にしたかったものの、長年培われた開発スタイルに切り込んでの改革は、簡単ではなかったといいます。
「技術的には充分可能ですし、変える努力はしてきたのですが、社内の意識がなかなか変わりませんでした。今のままでも新しい製品は生み出せているし、競争力も決して低くない。『このままでいいじゃないか』と思ってしまう現場の気持ちも分かります。こうしたマインドを社内だけで変えていくのは難しいと考えて、オーツー・パートナーズに支援をお願いすることになりました。」(西口氏)
CAEはあくまでも手段のひとつ。本当にめざすべきゴールとは?
オーツー・パートナーズの支援体制は4名のメンバーで構成されました。プロジェクトマネージャーの長嶺晋路は元大手自動車メーカー出身ということもあり、西口氏はその経験と知見に大いに期待していたといいます。「自動車業界では、CAEを活用したモデルベース開発(※3)の導入が進んでいます。そのノウハウをぜひ私たちに教えてほしいと思っていました。」ところが、長嶺からの最初のアドバイスは、意外なものだったそうです。
「私たちは一刻も早くCAEを定着させたい、と考えていましたが、長嶺さんから『CAEは目的ではなく、あくまでも“手段”です』といわれて、ハッとしました。一番大事なのは、設計で何をめざすのかということ。CAEはそれを実現するための道具なのだと、改めて気づかされました。」(津田氏)
めざすところを明確にし、開発にかかわるメンバーが同じゴールに向かって進める体制になっていなければ、CAEを有効に活用することは難しい。大手企業だからこそ、自分の専門以外の仕事が見えづらく、ワンチームになりづらかったことも、CAEの定着を妨げていた要因だったようです。そこで、設計のやり方を見直すことになりました。
※3 予め、システムの挙動を数理的に記述したモデルを作成しておき、モデルによるシミュレーションでシステムや部品の挙動を予測・検証する開発手法。詳しくはこちらMBD 投資が水泡に帰する要因|コラム|オーツー・パートナーズ (o2-inc.com)
設計前の「前さばき」で、製品の全体像をとらえる
上流からCAEを活用するには、開発にかかわるメンバーが、製品の機能全体を俯瞰してとらえていく必要があります。そのために、まずは設計前の「前さばき」から着手することになりました。オーツー・パートナーズからは、「技術ばらし(※4)」「品質機能展開(QFD)(※5)」「機能ブロック図(※6)」「要素ブロック図(※7)」「P-diagram(※8)」の5点セットを用意しましょうという提案がありました。これがあれば、各機能の関係性や機構や制御の仕組みなどの全体像を把握することができます。
「この機能設計5点セットを作成したことで、エンジニアとして仕事の見え方・解像度がガラッと変わりました。それまでは、自分が担当する範囲を超えた機能開発は誰がどのような仕様を設定し、どこまで検討を進めているのか把握するのが難しかったです。
例えば、同じ家電の開発でも、デバイスの担当は部品単品の個別最適化を、機能ソフトの担当は旧デバイスを用いたシーケンス変更を、互いに与える影響を把握せずに並行開発するため、後になって頑張る方向が違っていたことに気付き悔いるケースもありました。この5点セットを用いれば、自分の担当する部分の改変が製品のどの部分に影響するかをリアルに把握できるので、影響部分の担当部署とコミュニケーションを取る機会も増えました。」(内山氏)
お互いの仕事が見えるようになったメリットに加えて、今回の開発で得た成果やリスクを次に繋げる仕掛けができたことも、重要なポイントだったと内山氏は分析します。
「紙の資料やExcel・Wordなどに落とし込んだとしても、後日これらのドキュメントに目を通すのは大変なこと。その点、この5点セットはマスタ管理を行い共有化したこともあって、関係者の目に触れやすく確認も容易です。次の担当者に引き継ぐ時や外部設計とのやりとりにも、ここにアクセスすれば、過去の検討内容や失敗事例など気を付けるべきポイントが分かる。つまり経験の浅い若手もリスクを勘案しながら新機能の開発にチャレンジしやすくなり、上司はそれに対する判断をしやすい。非常に価値のあるツールになりました。」(内山氏)
しかし、技術ばらしや機能ブロック図のつくり方など、最初はなかなかポイントがつかめず、苦労したと西口氏は振り返ります。
「私たちが悩んでいるときも、オーツー・パートナーズのみなさんは熱心に、分かりやすい粒度にかみ砕いて教えてくれました。」
また、プロジェクトの途中からは、長嶺をはじめとしたオーツー・パートナーズのメンバーが同社に常駐するようになりました。
「ダメ元で長嶺さんに、“弊社に常駐してくれませんか“とお願いしたら快諾してくれまして。近くにいて、質問にすぐ答えていただける体制をつくってもらえたのは、ありがたかったです。チーム体制で、臨機応変に支援してもらえたことに、本当に感謝しています。」(西口氏)
※4 要求・機能・論理・物理の繋がりを可視化する図解手法。
※5 機能と物理の関連の強弱を数値化し、互いの影響度を可視化する手法。
※6 エネルギー源・情報源(入力)と最終形態(出力)の間を各機能間の入出力関係で繋げた図解手法。
※7 製品の物理的構成要素をブロックで示し、要素間のエネルギーや情報の授受を示した図解手法。
※8 入力・機能・出力・制御因子・誤差因子を可視化する図解手法。
『10年経ってもなかなか変わらない』と言われてきたマインドチェンジを1年半で
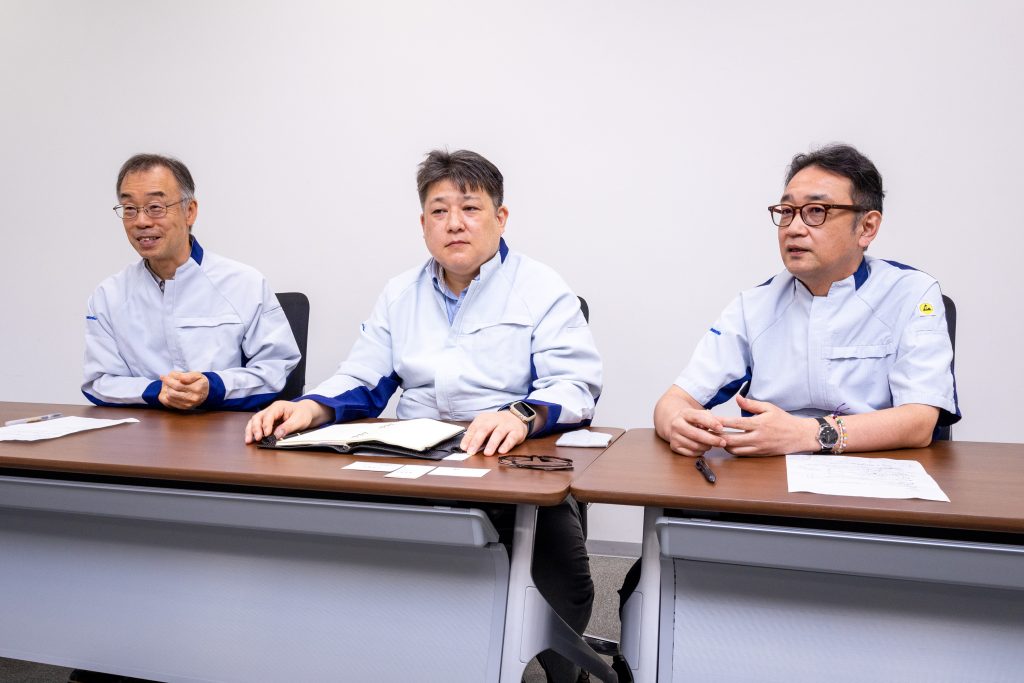
一方、事業部門には「CAEを使うより、実機でテストした方が早い」という意見も根強くありました。本部は、その意識改革にも取り組んでいきました。「オーツー・パートナーズから学んだことを活かして、変化を押し付けるのではなく、話し合いながら共通理解を深めていきました」という津田氏。
「CAEで解析した方が早い場合もあるでしょうし、実機でテストしたほうが良い場合もあるでしょう。どの手段を選べば、より早く、効率よくゴールまでたどり着けるか。そういう視点から考えましょう、という話をしていきました。そのうちに、『もっとこうしたら良いのでは?』という意見も事業部門から出てくるようになって。チーム一丸となって取り組もうと、本部も含めたみんなの意識が変わってきたことに手ごたえを感じました。」(津田氏)
「そうした努力の甲斐があり、『10年経ってもなかなか変わらない』といわれてきた現場のマインドが、わずか1年半のプロジェクトを経て変化の兆しがみられるようになりました。5点セットによって全体像が見え、自分の役割をはっきり認識することでエンジニアの仕事に対する姿勢が変わり、自らアイデアを出して積極的にチャレンジする若手が増えてきたと聞いています。『若手の目がキラキラしてきたよ』なんて上司の声も……。」(西口氏)
「今までは、機構、制御、実験など、それぞれに専門的なCAE領域があって、個別の取り組みをしていました。でも本来はバラバラではなく、全体でつながるべきものなんですよね。それが、今回のプロジェクトで明確になり、現場の理解も深まりました。そこが一番大きな成果だったと思います。」(津田氏)
「また、オーツー・パートナーズがちょうどいい距離で伴走してくださったので、『自分たちで考えて、行動に移す』という体験ができたことも、うれしかったですね。これまでも、コンサルティング支援に入っていただいたこともありましたが、弊社の風土として残り続けるような成果が得られることはあまりありませんでした。今回のプロジェクトでは、そこまでしっかり踏み込むことができた。オーツー・パートナーズにお願いして、本当に良かったです。」(西口氏)
最後に、みなさんに今後の目標を伺いました。
「今回のプロジェクトで培った成果をすべての家電の開発現場に展開し、ECMプロセス全体を変革することが目標です。法規の制約などもあり、完全な試作レスは難しいかもしれませんが、デジタル化を早急に進めて、遅くとも2030年までには、これまでのやり方を大きく変革したいですね。」(西口氏)
「今、社内では“Make New“という、既存事業の枠を超えて『未来の定番』を創出する全社活動が盛り上がっています。今回のような合理的で面白そうな取り組みに『真似させてよ』と人が集まり改善と称賛を繰り返すのがパナソニックの風土。本部と事業部門の行き来も活発なので、意外と早くイノベーションを起こせるのではないかと期待しています。」(内山氏)
大企業から中小企業、地方のスタートアップ企業まで、
幅広い支援事例から代表的なものを紹介いたします。
他の事例はこちら
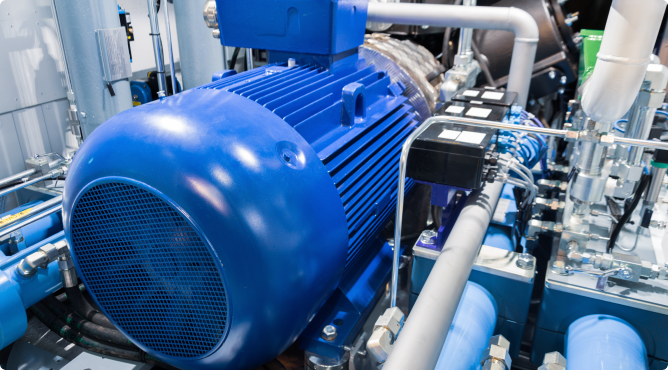
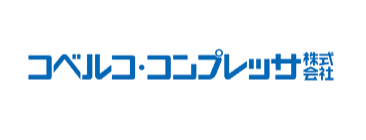
業種 |
|
---|---|
支援内容 |
|
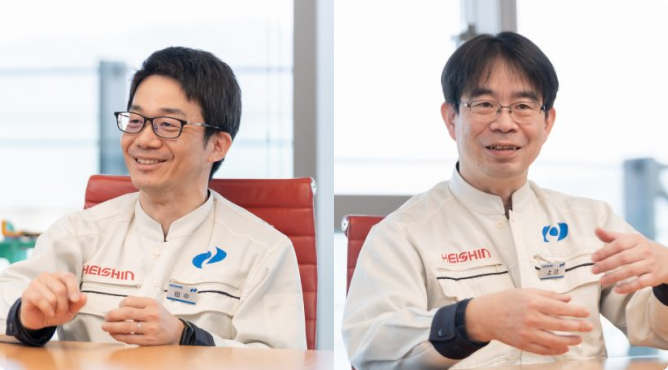

業種 |
|
---|---|
支援内容 |
|
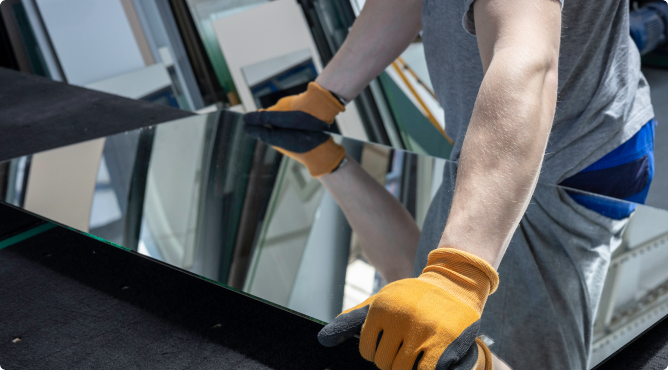
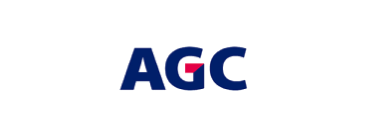
業種 |
|
---|---|
支援内容 |
|