独Industry4.0の今とこれからの日本 ~ドイツ生産自動化最前線から読み解く日本製造業のDX~【ウェビナー紹介】
- ウェビナーレポート
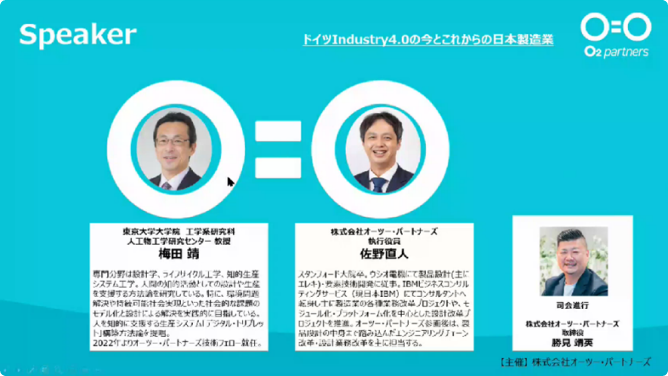
目次
株式会社オーツー・パートナーズでは、「製造業DX Webセミナー2022」の第1弾を開催しました。弊社執行役員の佐野直人が2022年9月にドイツを視察して見聞きしたIndustry 4.0の最新動向をご共有するとともに、弊社が日本の製造業DXを推進するものと期待する生産システム「デジタル・トリプレット」について提唱者の梅田靖氏(東京大学大学院工学系研究科人工物工学研究センター教授)からご紹介しました。本稿では、その模様を詳しくお伝えします。動画もご用意していますので、併せてご覧ください。
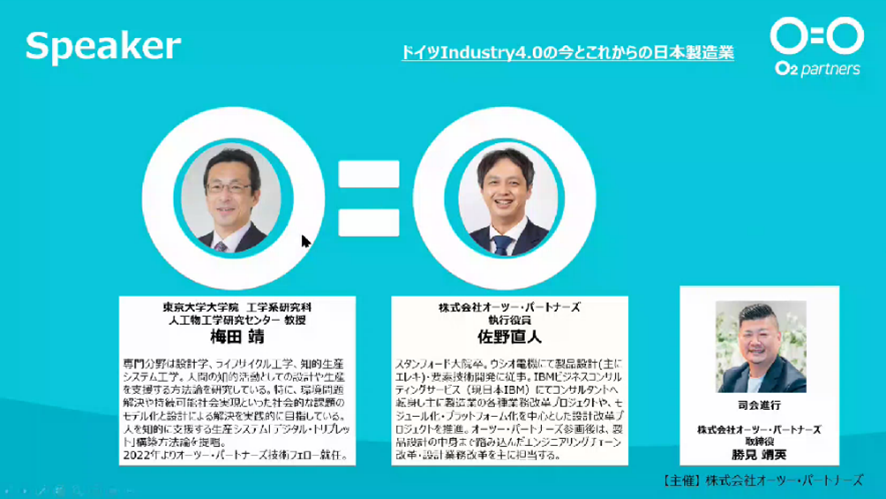
ドイツIndustry4.0の今~ドイツ生産自動化最前線
最初のセッションでは、オーツー・パートナーズでコンサルティング部門の総責任者を務める佐野から、ドイツが推し進めるインダストリー4.0の最新情報が共有されました。
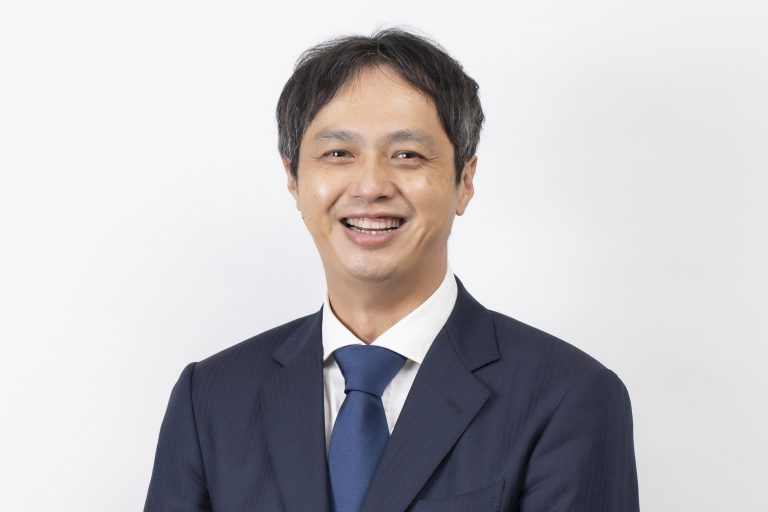
佐野:2022年9月、ドイツ商工会議所の企画で、ドイツのロボティックス関連企業団体とのネットワーキングの場がありました。ドイツを訪問して見聞きした情報をもとに、Industry 4.0の今と私の理解を共有させていただきます。
1 ドイツと日本の比較
よくドイツと日本は非常に似ている国だと言われますが、ここで改めて比較してみましょう。(データは2021年)
面積はほぼ同じですが、人口は日本のほうが多く、ドイツの約1.5倍です。生産年齢人口の比率についても大きな違いはないものの、ドイツがやや多い状況です。GDP(ドル換算)も大きな開きはありません。2021年時点では日本のほうが多かったのですが、2022年は円安の影響もありドイツが上回ったようです。
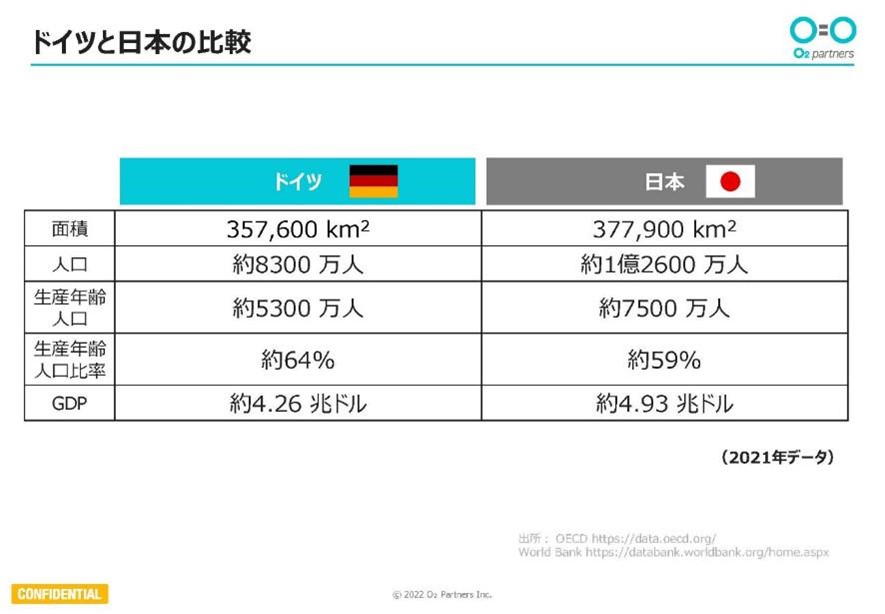
生産年齢人口(15歳~65歳未満の人口)の推移について見ていきましょう。今後は両国ともに引き続き下がっていきますが、ドイツのほうが急激に変化し、差は縮まりそうです。つまり、生産力に関する課題は近しいものになると考えられます。
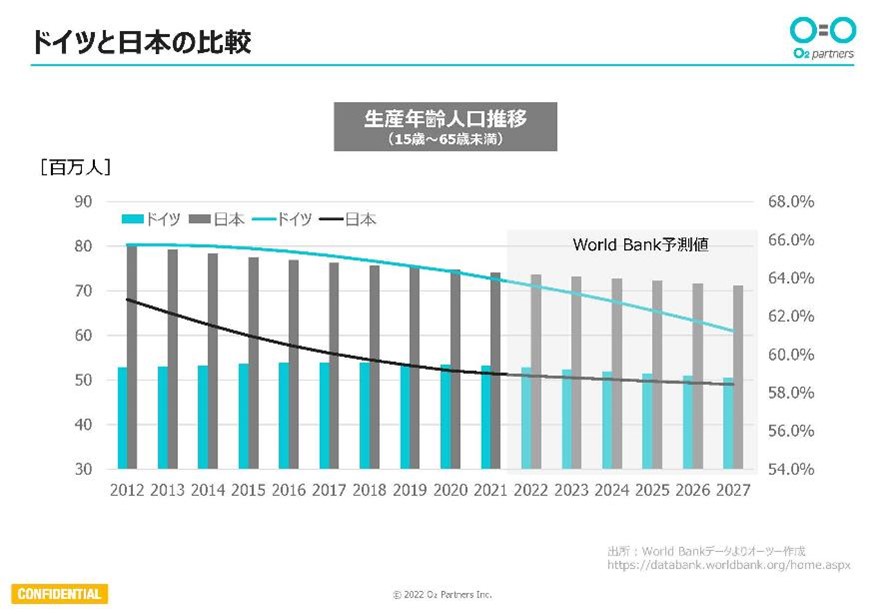
続いて、労働者数を産業別で比較してみましょう。両国とも製造業の割合がもっとも多く、ドイツは約800万人、日本は1000万人となっています。日本は卸売・小売の比率が高くなっていますが、全体的には似た構成だと言えるでしょう。
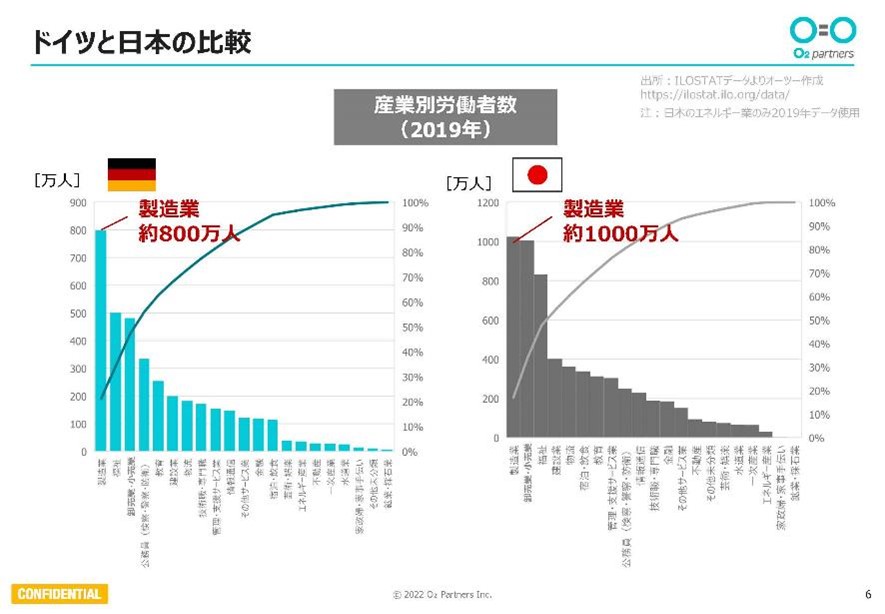
2 Industry4.0の概要とドイツの現状認識
ここで改めてIndustry4.0の概要を整理しておきます。これまでの産業革命は主に蒸気機関、電力、コンピューターといった核となる技術の登場に伴うものでした。
そしてIndustry4.0では、「サイバーフィジカルシステム」が登場しました。フィジカル空間の情報をサイバー空間に吸い上げて分析し、その結果をフィジカル空間に戻すことで生産を大きく変えていく仕組みを、ドイツをはじめ各国が作ろうとしています。
情報通信技術を活用して、産業用の機械やプロセスをインテリジェントにネットワーク化するIndustry 4.0では、自由度の高い生産、組み替え可能な工場、サーキュラーエコノミーなどの実現が期待されます。
さて、Industry 4.0を提唱したドイツでは、ドイツ自身の現状をどのように認識しているのでしょうか。2021年に発行されたbitkom(ドイツIT・通信・ニューメディア産業連合会)のレポートでは、加盟している経営者、製造部門トップへのヒアリング調査がまとめられています。
進捗状況については、95%の企業がIndustry 4.0をチャンスと捉えており、83%の企業はIndustry 4.0のアプリケーションをすでに使っているか、使う計画があると回答しています。
一方で、66%の企業はIndustry 4.0の取り組みが遅れている、あるいは取り残されていると感じています。
では、何がIndustry 4.0を阻害しているのでしょうか。もっとも多いのが「資金不足」(77%)で、「データ保護にかかわる要件を満たせない」(61%)、「ITセキュリティにかかわる要件を満たしていない」(57%)、「スキルを有する人材の不足」(55%)、「テーマが複雑でどうすればよいか分からない」(52%)と続きます。このような課題を挙げる企業の多くは、中小企業でした。
このレポートでは、「製造業の大部分、ひいてはドイツ経済の心臓部が、遅かれ早かれ競争力を失う危機にさらされており、ドイツの成長と雇用への影響は深刻」とした上で、「特に中小企業の投資に対する障壁を克服することが課題」だという認識を示しています。
このような課題認識のもと、中小企業向け支援が行われています。その1つがロボティックスの分野で、ICMという団体が多彩なメンバー企業を集めて研究開発のプロジェクトマネジメントをしたり、ビジネスモデル開発から市場投入までをサポートしたりしています。
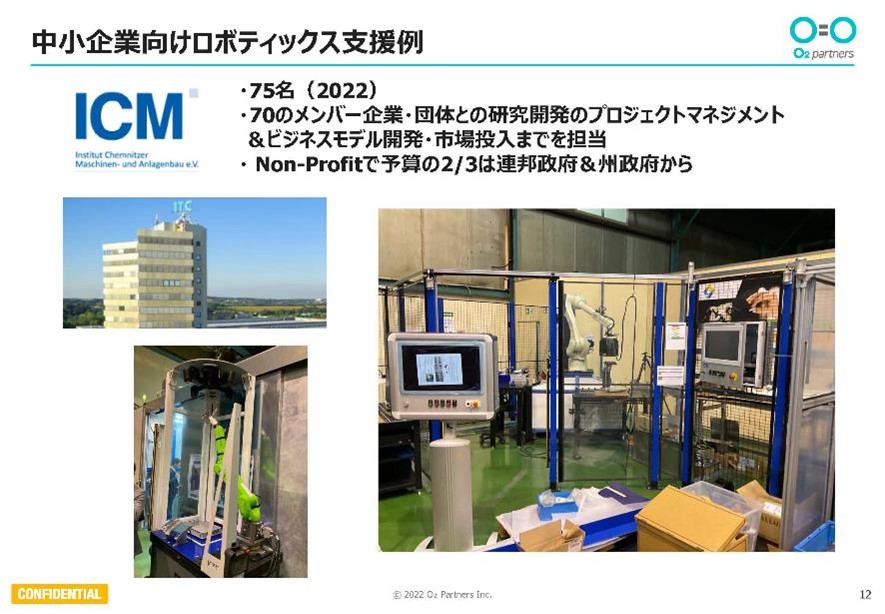
3 ザクセン州紹介
今回の視察で訪れたザクセン州についても、簡単にご紹介しておきます。ドイツの東部に位置する、人口約410万人の州です。この10年ほどドイツでの成長率が第2位の州で、成長性のある土地です。
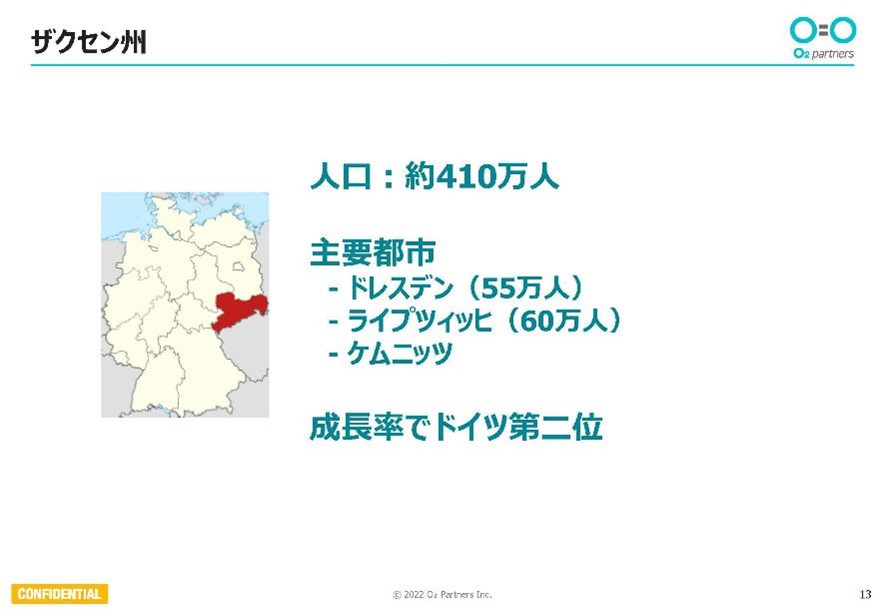
日本企業も多く進出しており、半導体やロボティックス関係の企業が多く所在しています。
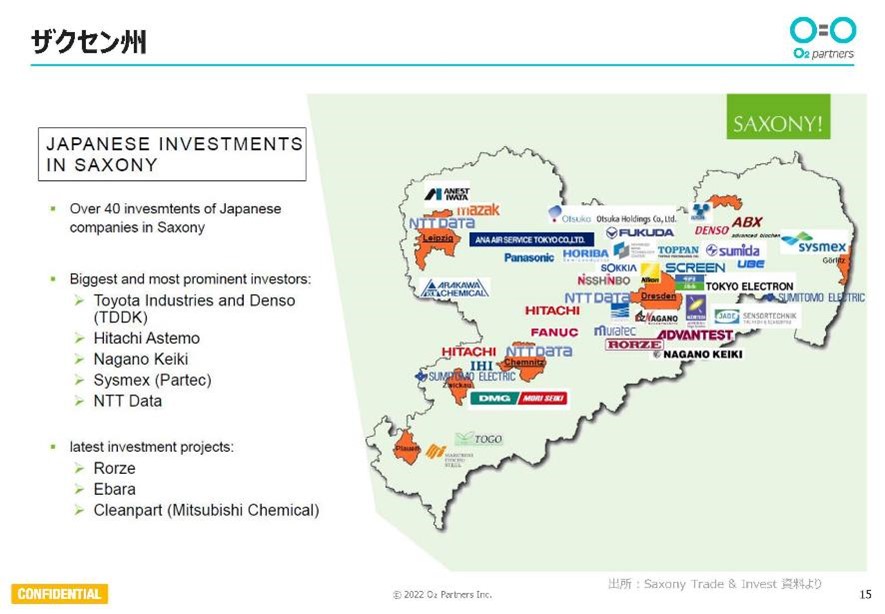
ザクセン州で最近、大きな注目を浴びているのがBOSCHの半導体工場です。BOSCH初のAIoT工場で、工場全体がデジタルツイン化されているため、製造・保守のプロセスをリアルタイム分析し、自己最適化アルゴリズムによって生産性をどんどん向上させることが可能です。2021年だけで10億ユーロの投資が行われています。
4 Industry 4.0の推進に向けた取り組み事例
ここからが、本題であるザクセン州からの報告です。
スタートアップクラスターと大企業の連携
ザクセン州では、スタートアップ、新興企業、中小企業をネットワークで結びつけたクラスター(集団)が、大企業と連携してモノづくりにあたる取り組みが推進されています。
中心的な役割を担うSmart Systems Hubは、企業や団体をつなぐハブの役割を果たし、新しいモノを作りだしていくためのプロジェクトマネジメントやプロダクトマネジメントを行う企業です。その周りには、キーパートナーとして大企業のInfineon(半導体ソリューション)、SAP(ソフトウェア)などが参画しています。また、シェアホルダーとして、ドイツの半導体導入を推進する団体や、5Gを推進している団体があります。そしてIoT関連の中小企業が500社以上、スタートアップ企業は200社以上が参画しています。
例えば、A社が取り組みたいテーマや解決したい課題について、Smart Systems Hubへ相談したとします。Smart Systems Hubは同社のネットワークの中から、どんな企業や団体を結びつければゴールへ導けるかを考え、うまくつなぎ合わせてプロジェクトを形成します。そしてモノを作ってA社へ納めるところまで責任を持って遂行する、そんな事業を行っています。
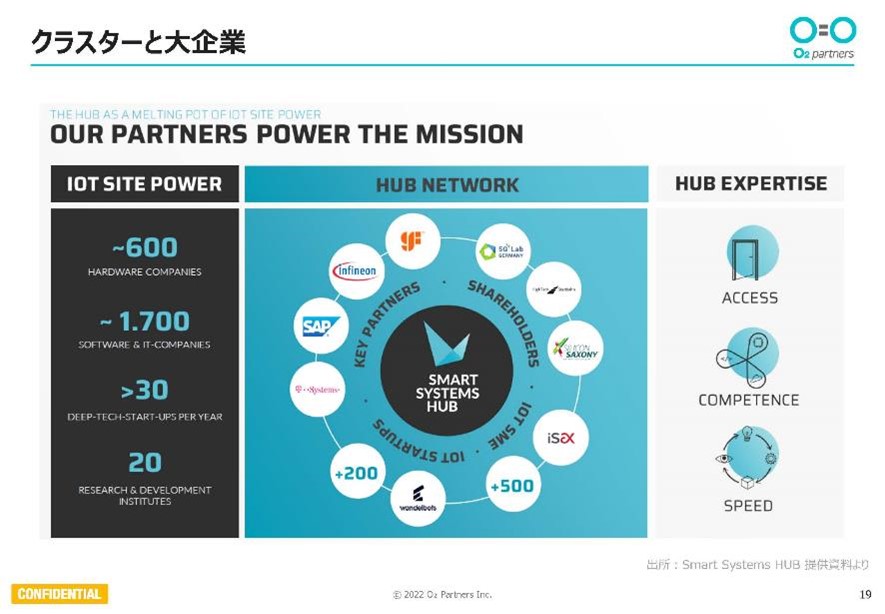
大企業であれば、自分たちだけで完結できるプロジェクトもあるでしょう。それでもSmart Systems Hubを窓口に外部の協力を得ようとするのは、より広い知見や新しい情報を集めたいと考えているからです。
ザクセン州はロボティックスとIoTに力を入れており、ハードウェア企業が約600社、ソフトウェアやITの企業が1700社、この地で事業を行っています。他にもディープテックやスタートアップの企業が毎年30社ほど誕生。Smart Systems Hubは、このような環境をうまく活用してネットワークを構築し、新しい価値を提供しています。
-Smart Systems Hubのプロジェクト事例-
Smart Systems Hubが関わったプロジェクト事例を2つご紹介します。
1つ目は、バルブの予知保全を実施するためのセンシングデバイスを作った取り組みです。ベースとなる技術はエッジコンピューティングとセンサーで、通信技術を組み合わせて新しい機器を作り、あわせてサービスモデルも作りました。
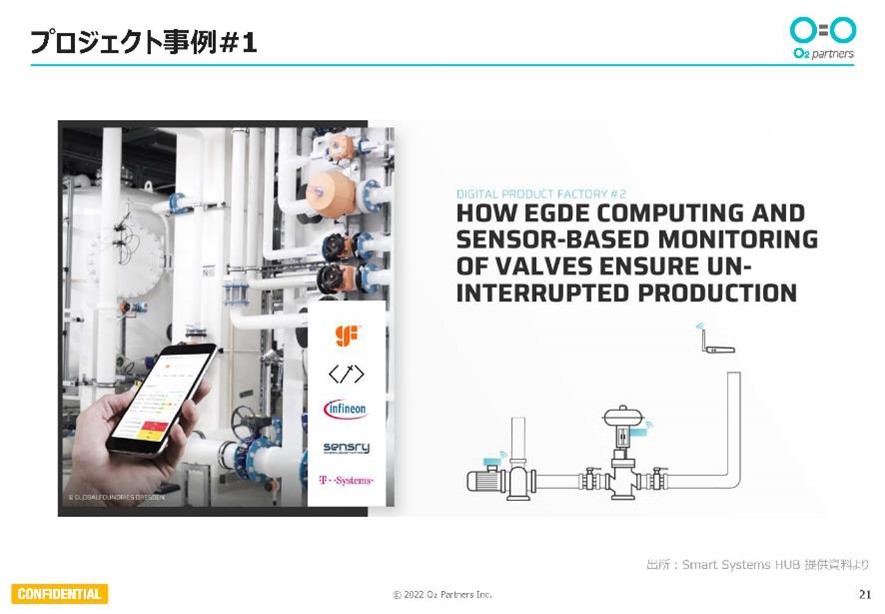
この取り組みのオーナー(チャレンジオーナー)はアメリカの半導体企業GlobalFoundriesで、プロジェクト全体の資金を提供してプロダクトを作り上げていきます。Smart Systems Hubはプロダクトオーナーとして、開発の中心的役割を果たします。Infineonがセンサーを提供し、Sensryがマルチセンサープラットフォームを提供。他にも組み込みソフトの技術力やエッジAIを提供する企業など、さまざまな役割を持つパートナーをSmart Systems Hubが集め、チームを編成してモノ作りを進めていきました。
2つ目は、協働ロボットにAIセンサーを取り付けることで、ロボットを売って終わりの売り切りモデルから、ロボットの性能を切り売りして利用料を得るモデルへの転換を図るプロジェクトです。ビジネスモデルの開発とモノの開発を並行して進めていきました。
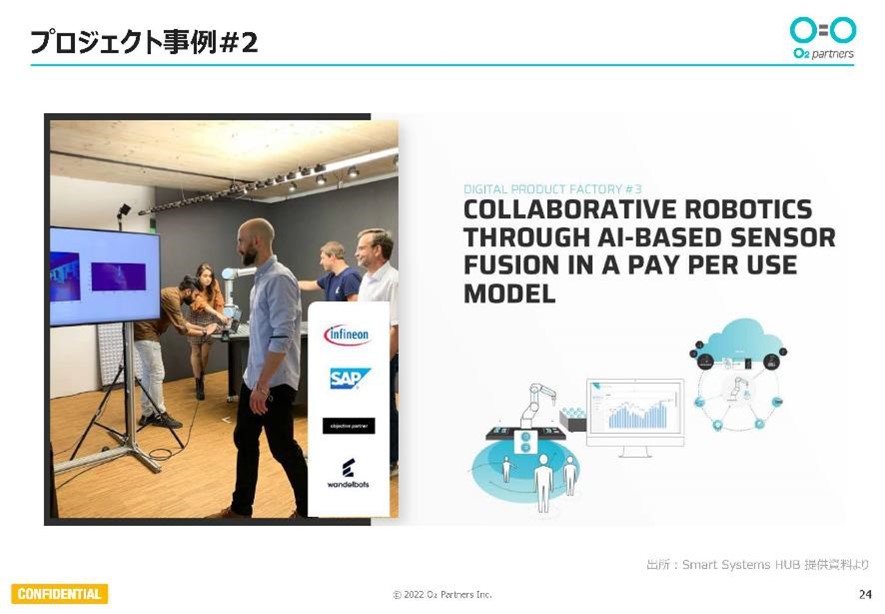
このプロジェクトのチャレンジオーナーはInfineonで、資金を提供してモノ作りを進めていきます。そしてSmart Systems Hubがハブとなって、SAP(クラウドインフラ)やWandelbots(ロボティックスインフラ)といった会社を集めました。
Infineonは、この他にも工場の生産性向上のためにロボットの製造をSmart Systems Hubに依頼するなど、かなり意図的にスタートアップ企業を利用しています。
-ドイツ各地に広がるハブ企業を中心に据えた価値づくり-
現在ドイツには、Smart Systems Hub同様にハブとなる企業が12社あります。ハンブルクではデジタルロジスティックス、ベルリンではフィンテック、カールスルーエはAI、ニュルンベルクではデジタルヘルスといったように、地域ごとに特色あるハブ企業を置き、その周りにスタートアップ企業を生み出し、地域として新しい価値を作っていこうとする取り組みが進められています。
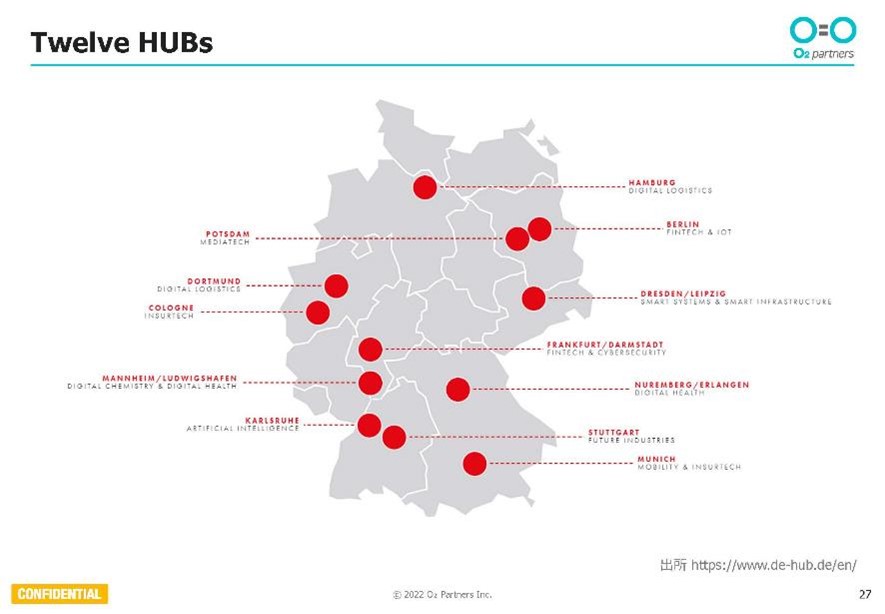
今回の視察では約10社を訪問しましたが、必ず耳にしたのが「ネットワーク」「クラスター」といった言葉です。こうした取り組みを各企業がうまく使っていこうとしていることを強く感じました。その意図を改めて考える際に参考となるのが、Infineonの考え方です。同社のウェブサイトにはスタートアップ企業と協力することのメリットが記されていますので、引用してご紹介します。
Infineon「スタートアップ企業との協力契約のメリット」
インダストリー4.0およびコボット分野の発展に追随するために、また、デジタルの未来を築く積極的役割を担い続けるために、インフィニオンは、スタートアップ企業との協業を進めています。スタートアップ企業は、有名企業があまり持っていない資産、すなわち厳格なプロセスが必要なために扱いにくい資産を持っている場合があります。
- 顕著な創造力
- デジタル化進展のための新たなアイデア
- 延々と続く調整の繰り返しのない、迅速で実際的なアプローチ
- 既存の枠にとらわれない自由な思考
コボット…協働ロボット
ロボティックス活用拡大に向けた革新技術の紹介
ロボティックスを普及させていくためには、いかにシンプルに導入を進めるかがポイントです。そこで、中小企業にとって参考になる2社の取り組みをご紹介します。
1社目は、ロボットティーチングの革新技術を持つWandelbotsです。設立は2011年で、123Mドル以上の資金を集めたことからも、かなり成長性が高いという評価を受けていることが分かります。
ティーチングを行うシステムはロボットメーカーごとに異なり、それぞれにティーチングのノウハウがあります。また、ティーチングのための言語についても、それぞれ理解する必要があるなど、簡単ではありません。ティーチングの人材は不足しているため、ロボットの立ち上げが遅れることも珍しくありません。このような状況を、新しい技術で解決していこうと取り組んでいるのがWandelbotsです。
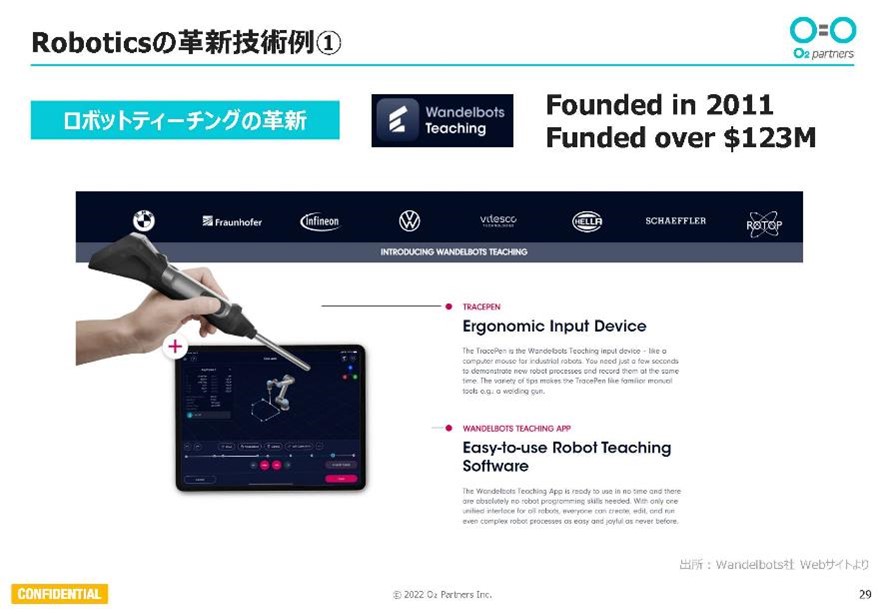
Wandelbotsの公式YouTubeでは、溶接と接着剤の塗布を行うロボットをティーチングする様子が紹介されています。
ペン状のインプットデバイスを使ってトレースすることで、ロボットは学習し、人の手と同じように動くパスが自動生成されます。細かな調整はタブレット上の使いやすい画面で行えるのも特徴です。
ロボットのティーチングは、実際にやってみると相当手間がかかります。そのことがロボット導入の阻害要因になっているのではないでしょうか。実際に画面を見ましたが、かなりよくできたUIで、これでティーチングが終わるのであればかなり便利だなという印象を受けました。
設立して10年が経った現在、ドイツ国内ではフォルクスワーゲンやBMWといった企業でも導入されています。ドイツ以外の国でもかなり実績ができているようです。
2社目は、工場内通信の革新に取り組むMeshmerizeです。工場内ではよく産業用のWi-Fiが使われますが、ロボットの稼働に適した技術ではありません。ロボットが動き回って物影に隠れた場合などには、産業用であっても電波が途切れてしまいます。Meshmerizeは、オフィスなどで使われる一般的なWi-Fiをうまく活用して、工場内でもクリアな通信を実現する技術を開発しています。ロボット同士がWi-Fiを中継しあいながら補うという発想で、遮蔽の影響なくスムーズにロボットが稼働する工場を実現しようとしています。2021年に設立したばかりなので、現在は市場への投入に向けた取り組みを始めている状況です。
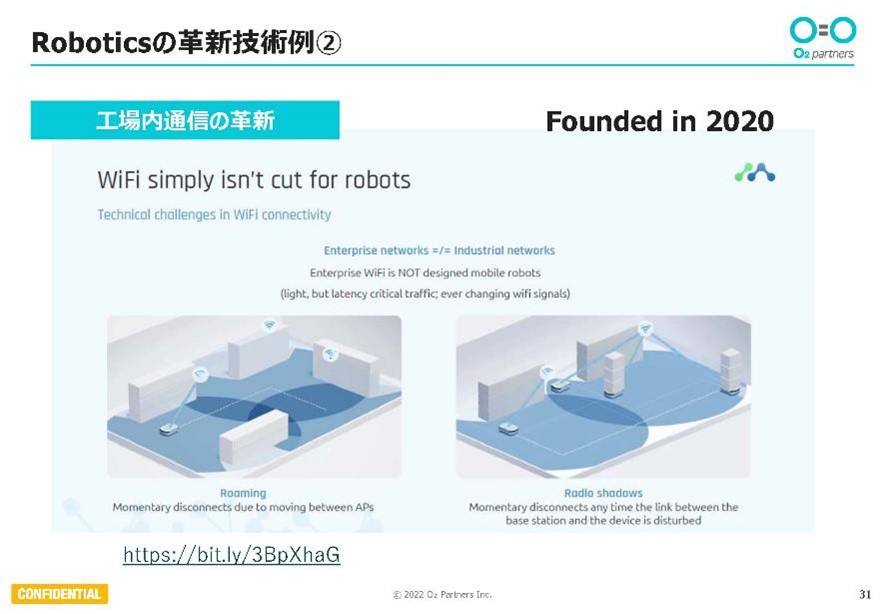
この2社以外にも、ロボティックスの導入をシンプルにしようと取り組んでいる企業があります。Smart Systems Hubが間に入ることで、こうした個々の企業が持つ技術を活用した新しい課題解決のソリューションを作りだそうとしているのが、ドイツにおけるIndustry4.0の動きです。非常にうまく回り始めているなという印象を持ちました。
Fraunhoferについて
最後に、フラウンホーファー研究機構の動きについてもご紹介します。欧州最大の科学技術分野における応用研究機関で、民間企業や公共機関向けに実用的な応用研究を実施しています。ドイツ国内で76の研究所を持っており、全体の年間予算は約29億ユーロ(約4200億円)、職員数が約3万名(うち研究員は2万名強)の団体です。
今回私が訪問してきたのは、工作機械・成形技術研究所(IWU)で、ケムニッツとドレスデンに拠点を持っています。こちらの年間予算は約4800万ユーロ(約71億円)、職員数は約670名です。予算のうち半分強は企業との連携によって獲得しているそうです。
フラウンホーファー研究機構は、日本であれば産業技術総合研究所(産総研)に相当するのではないでしょうか。そこで両者を比較してみました。産総研の職員数は10分の1など、規模の違いは鮮明です。特徴的なのが財源で、フラウンホーファー研究機構では7割以上が民間企業の委託契約や公共財源による研究プロジェクトで賄われているのに対し、産総研は7割が交付金や補助金によるものです。
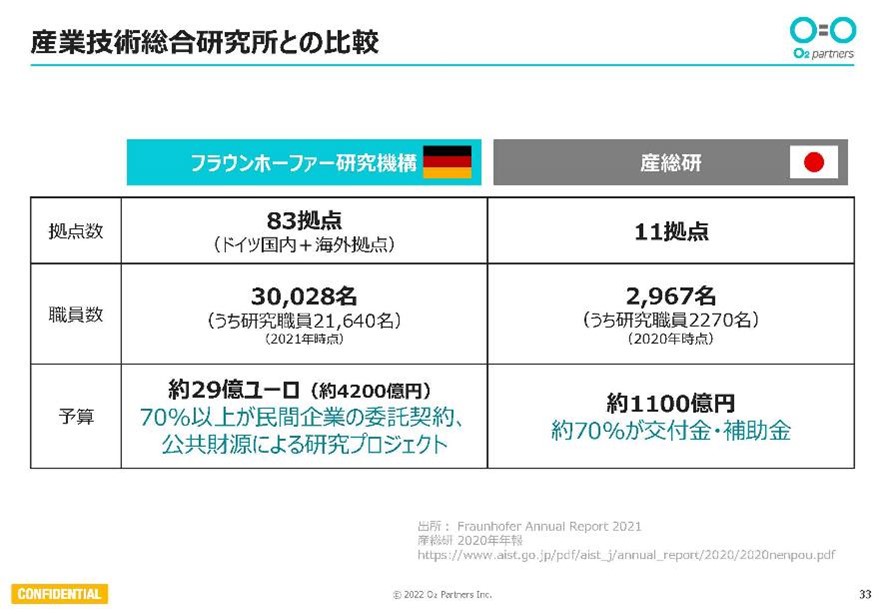
76拠点で非常に多岐にわたる研究開発をしているフラウンホーファー研究機構ですが、その中で多いのが自動車業界に関する研究所です。特にフォルクスワーゲンとの関係が強く、要素技術の開発や自動車プラットフォームの策定においてフラウンホーファーが深く関与しています。
要素技術開発では、例えばジェスチャーコントロールがあります。ジェスチャーで工場のロボットと連携して生産性を上げるような取り組みを行っています。
プラットフォーム策定では、フォルクスワーゲングループの自動車プラットフォームMQBや、その派生である電気自動車プラットフォームMEB上で、混流自動化ラインの構想を行ったり、ライン設計の一部を担ったりしています。今後はフラウンホーファーがプラットフォーム策定にも関与するなど深く入り込んでいき、自動車の設計をもとにライン設計を自動化する取り組みを進めるそうです。
このように、フラウンホーファー研究機構では、中小企業だけでなく大企業との取り組みも行われています。また、要素技術開発の過程では、ハブになる企業の工程を一部担うことも。自動車メーカーとフラウンホーファー、そしてスタートアップのハブがうまく連携して回っています。
世界デジタル競争力ランキングに見る日本の製造業におけるDXの課題
続いては、司会進行を務めるオーツー・パートナーズの勝見が、世界デジタル競争力ランキングを紐解き、日本の製造業におけるDXの課題を提起します。
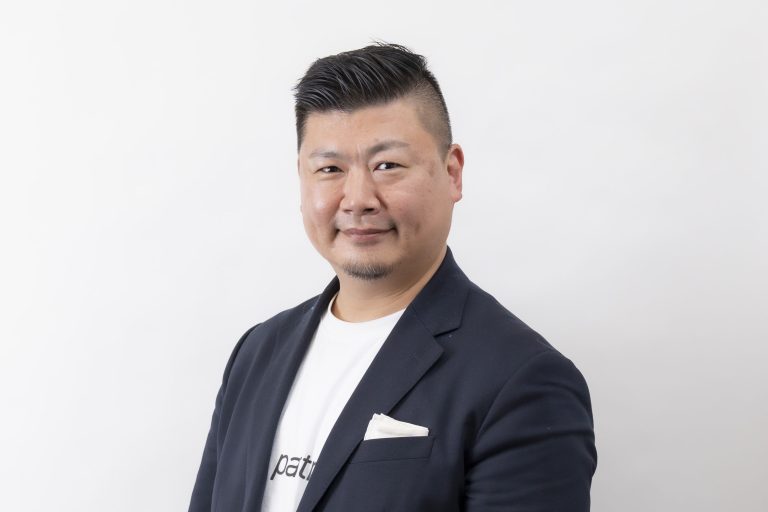
勝見:スイスのIMD(国際経営開発研究所)が毎年秋に発表する世界デジタル競争力ランキング、2022年の日本は29位で、2018年の22位から毎年ランクダウンしています。一方でドイツは19位と、近年は10位台後半を常に維持しています。ドイツはIndustry4.0発祥の地ですから、もっと上位のようなイメージがあるかもしれません。
2022年の1位はデンマークでした。これまでも上位に位置していたデンマークが、GAFAMを擁する不動のアメリカを抜き、ついにトップをとりました。
日本以外のアジア勢を見てみると、シンガポールの4位を筆頭に韓国、香港が10位以内、台湾と中国も日本より上位に位置づけられています。
ご紹介したのは総合順位ですが、分解すると「知識」、「テクノロジー」、「将来への備え」の3大主要ファクターと、さらに9つのサブファクターに分けられます。
日本についてよく見てみると、10位以内のサブファクターがあるものの、大きな数字が目立ちます。「人材」が50位、「規制の枠組み」が47位、「ビジネスの機敏性」が62位などとなっています。
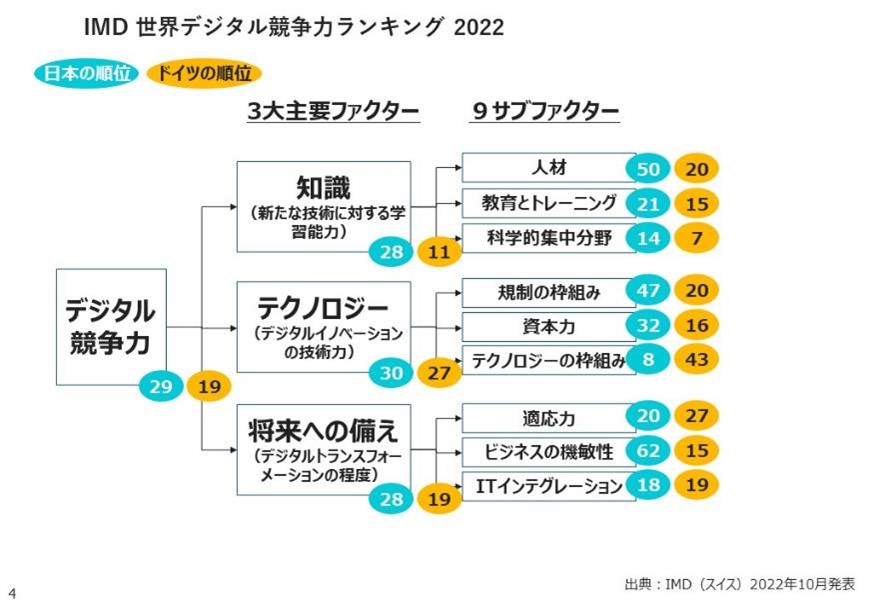
さらに分解すると51項目に分かれるのですが、「国際経験」が63位、「デジタル/技術スキル」が62位、「商機と脅威に対する企業の反応速度」が63位、「ビッグデータの運用と分析」が63位となっています。63カ国のランキングなので、63位は調査対象の国や地域で最下位だということです。
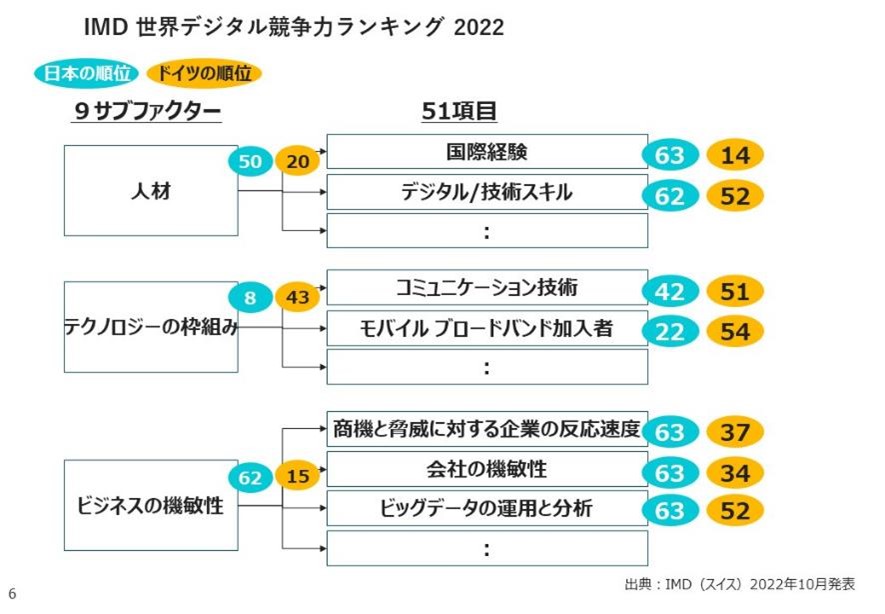
佐野から紹介したドイツの事例からは、そこまでイノベーティブな印象を受けなかったのではないでしょうか。日本でも、負けない革新技術を開発している企業はあります。「デジタル/技術スキル」や「ビッグデータの運用と分析」は、デジタルやデータの利活用で求められる技術力ではあるものの、まだ何とかなるのではないかと思っています。
一方で致命的なのが、「商機と脅威に対する企業の反応速度」や「会社の機敏性」といった企業の変革力に関する項目です。世界戦を勝ち抜くには、デジタル力だけでなく「変革スピード」が求められます。
この部分に着目してみると、ドイツも「デジタル/技術スキル」は52位で低い位置にいます。「ビッグデータの運用と分析」も52位です。日本よりも企業の変革スピードはマシ、といったレベルです。
実際に日本の製造業が競争相手として戦っているのは、ドイツよりも韓国やアメリカ、中国系の製造業が多いのではないでしょうか。そうした国の企業と戦うには、やはり企業の変革力やデジタルデータの利活用力が問われることになります。
デジタル・トリプレットとは
なかなか変われない日本の製造業において、DXを推進するためのアプローチとして梅田教授が提唱するのがデジタル・トリプレットです。
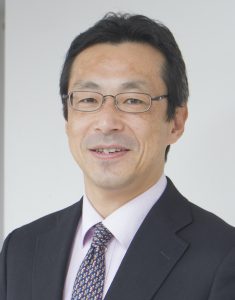
デジタル・トリプレットを提唱した背景
梅田:勝見さんのデジタル競争力についての分析はもっともです。企業の変革力が最下位というのが非常に痛いところで、私の実感とも合っています。これからご紹介するデジタル・トリプレットは、変革力を上げるためのものではないかもしれませんが、変革する気になった際にデジタル化をスムーズに進めるための方向性を示すものです。
日本でもIoTブームのときには、工場の中でデジタル化が進みました。例えば工作機械をIoTに対応させてログデータをたくさん貯めたという話はよく聞きます。ただ、それをどう使いこなして価値を生み出せばいいのか、よく分かっていないのが課題でした。
また、個社のやり方で取り組んでしまったために、Industry 4.0が目指すようなネットワーク化は実現できていません。ネットワークのプラットフォームは日本のメーカーも手がけており、機器間の接続や情報の流通経路としては役立てられていますが、そこにつなげた後、どのように付加価値を高めていくのかについては、なかなか見えてこないのが現状です。シーメンスのように豊富なソフトウェア群でエンジニアリングチェーン全体を支援するプラットフォームにはなっていません。
ただ、Industry 4.0を指向することが日本の製造業にとってベストだとは限りません。非常にうまい考え方だとは思いますが、ドイツ流の生産ラインでなければ価値を発揮できないのではないでしょうか。ドイツ流の生産ラインは、ホワイトカラーのエンジニアによるトップダウンの意思決定を前提に動かされており、作りには余裕を持たせてあり、そうそうは変わらない前提だと理解しています。
また、Industry 4.0は自動化による合理的な生産ラインを目指しています。先ほど佐野さんから、フラウンホーファーとフォルクスワーゲンが自動車プラットフォームにおいて生産ラインの自動設計を目指しているという紹介がありましたが、典型的な例ではないでしょうか。
それから、工場に適用したサイバーフィジカルシステムに対して、現場でカイゼン活動をすることは恐らく想定していません。日本の工場なら、現場で手を加えてチューニングしないと気が済まないはずです。
何が日本の強みなのかは、まだ明確ではありませんが、仮に現場の熟練者や生産技術者の質の高さや、日々のカイゼン、常にムダ取りをして日々成長する生産ラインだとすると、ドイツ流で生産ラインを自動化するという考え方とは背反するところもあるのではないでしょうか。
そこで私は、日本型のモノづくりの強みをデジタルの新しい器(IoT、サイバーフィジカルシステム、AIなど)に盛りなおす必要があると考えました。熟練者やエンジニアたちの能力を活用した、人間中心のデジタル時代のモノづくりの方法があると思っています。
デジタル・トリプレットとは何なのか
それがデジタル・トリプレット(D3)です。物理世界と情報世界からなるデジタルツインに、人が活躍する知的活動の世界を加えた3層構造になっています。知的活動世界では、エンジニアがデジタルツインをうまく使いこなしながら、製品ライフサイクルに価値を創出することで、エンジニアは能力を高めつつデジタルを使いこなせるようになると考えています。
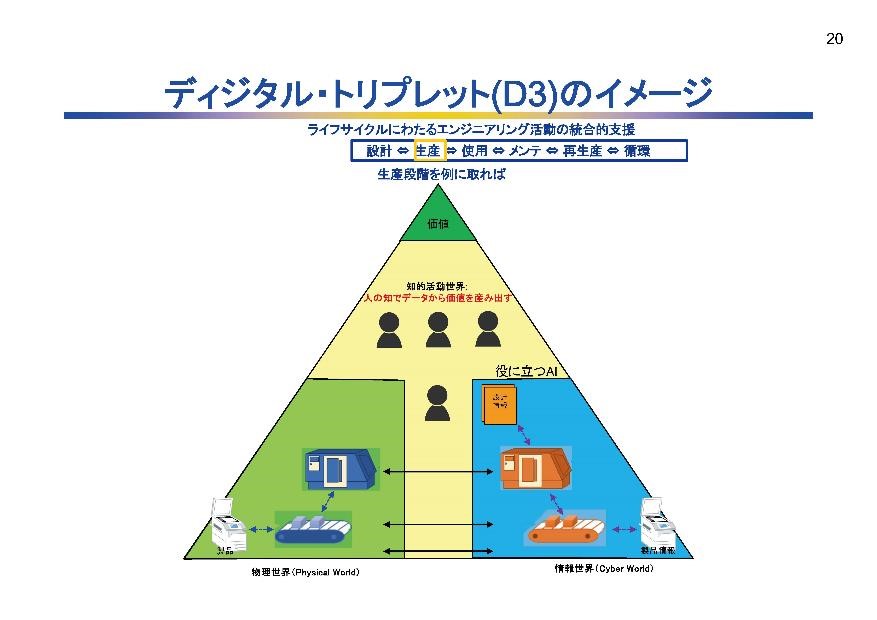
今後は現場のエンジニアもブルーワーカーも、デジタルを使いこなすことが必須になってくるでしょう。そして問題解決では、生産ラインからデータを収集し、さまざまなツールを使いながら分析・評価して、問題があれば対策を考えて実施することになります。これがデジタル・トリプレット上でのエンジニアリングサイクルです。
先ほど佐野さんから、ロボットのティーチングを容易にするWandelbotsの紹介がありました。溶接については、パスをかなり細かくチューニングしないと難しいのではないでしょうか。そのためのノウハウをデジタル・トリプレットのアプローチでうまく蓄積すれば、より品質の高い溶接のパスを作ることができるでしょう。
エンジニアたちが自発的に、状況に応じて行っている調整や注意していることがあるはずです。そのノウハウを彼らの中にではなくシステムとして貯めていくことで、デジタルの世界でもエンジニアリング活動は可能だと考えています。
デジタル・トリプレット上でエンジニアリングサイクルを回していくために、エンジニアはデジタルを使いこなすための能力が求められます。何を測るのか?(データ収集やシステムの構築)、何をどう分析するのか?(ツール選定、情報分析方法決定)といった知識を学んでおく必要があると思います。
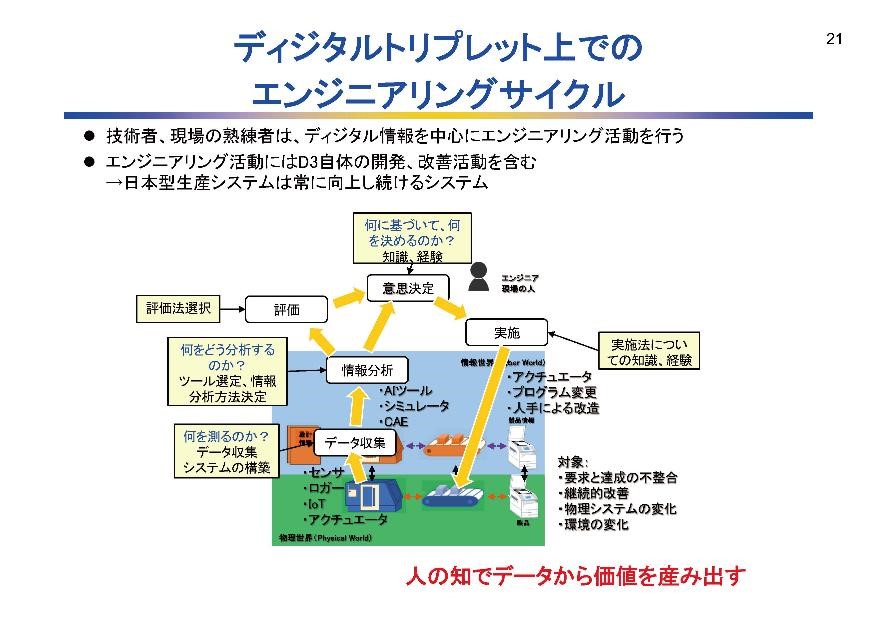
エンジニアたちの持つノウハウを蓄積するプロセスは、Industry 4.0のシステムでは組み込まれていないものと理解しています。デジタル・トリプレットでは、ノウハウをまず形式知化してプロセスを記録することで、エンジニアたちがいろいろなプロセスを作り始めるようになり、生産システムがスパイラルアップしていくものと期待しています。
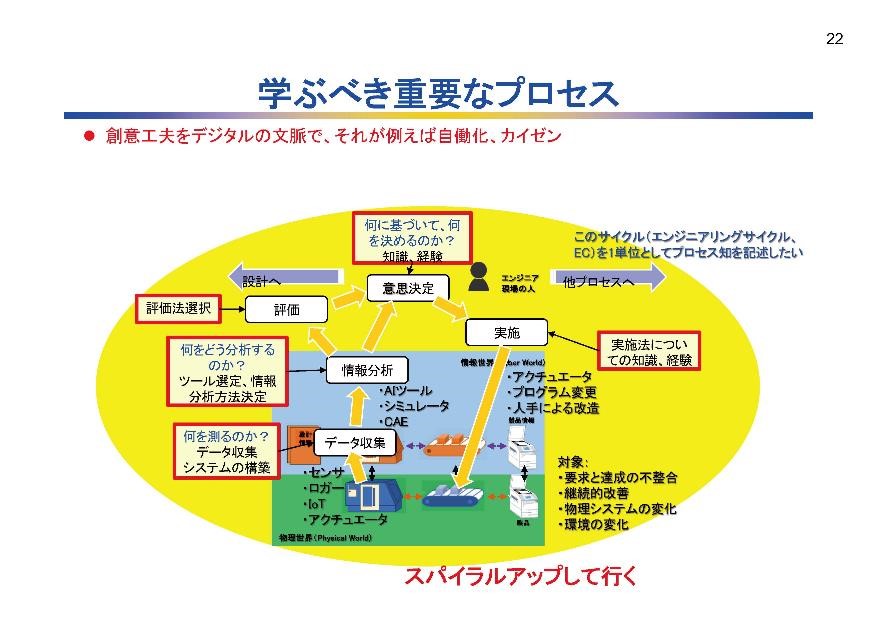
デジタル・トリプレットが目指すエンジニアリング支援
ただし、安定運用状態において自動でフレキシブルに生産し続けるには、Industry 4.0を継承すればよいでしょう。Industry 4.0のやり方は標準的で、アーキテクチャーもありますし、構成技術も豊富です。
一方でデジタル・トリプレットは、サイバーフィジカル生産システムの開発や設計、立ち上げ、そしてメンテナンスやカイゼンといった通常運転ではない場面において、エンジニアを支援するのが狙いです。
そこで現在、私たちはフィールドエンジニアたちの作業をナレッジエンジニアが観察してプロセスを記録し、そこから生産ラインの改善提案を行えるように一般化して、汎化プロセスモデルと呼ぶテンプレートや教科書のようなものを作る取り組みをしています。汎化プロセスモデルを使って、経験の浅いフィールドエンジニアを手助けするのです。
汎化プロセスモデルの利用を繰り返すうちに、AIを使うのが適切だとか、ソフトウェアで支援できるといったことが分かってくるので、図中のEサイクルでどんどんスマート化していきます。
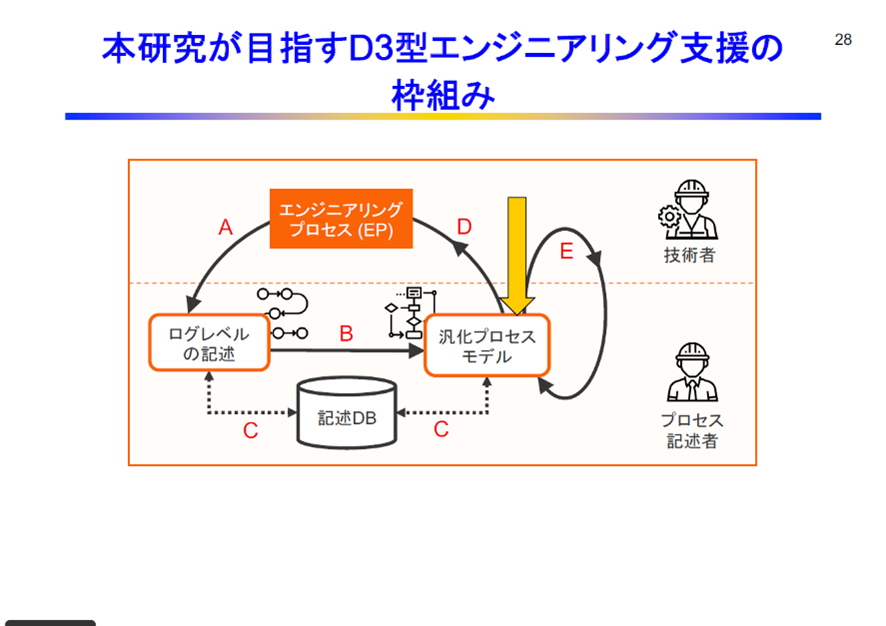
しかし、プロセスを適切に記録する手段がありませんでした。そこで私たちは作業を記録する言語「PD3(Process Modeling Language for D3)」を開発しました。PD3でエキスパートのあらゆる行動を書き下していきます。
PD3の特徴は2つあります。1つは、作業者の意図の記号的記述です。なぜその作業を行ったのか、インタビューによって抽出して記録します。
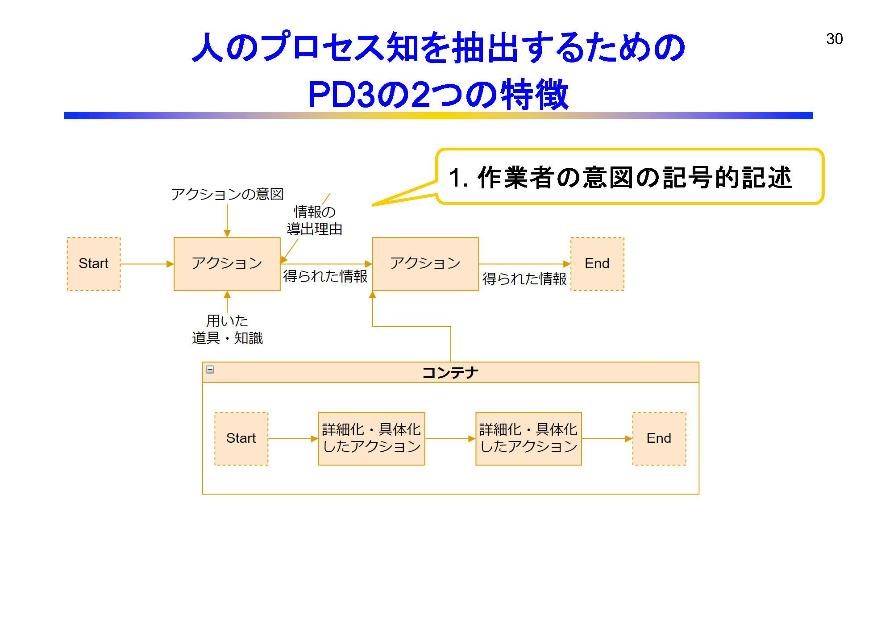
もう1つは、デジタル・トリプレットの3つの世界に対応づけて、アクションを3つに分けて記述するところです。そうすると最後には、ソフトウェアの操作や機械の操作に落ちることになります。
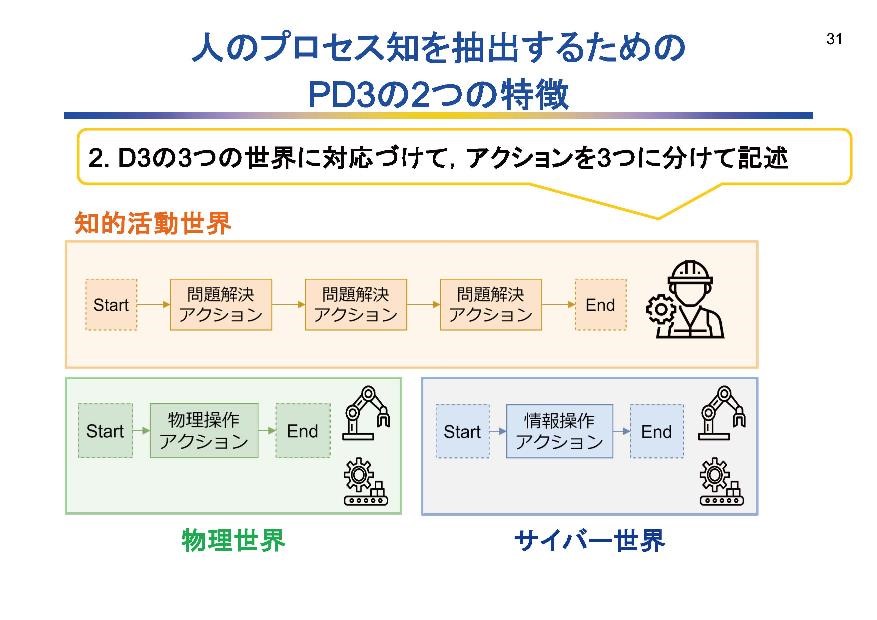
研究室におけるデジタル・トリプレットの実証
私の研究室や人工物工学研究センターには、LEGOとPLCやセンサーを組み合わせて作った自動組み立てラインと、そのデジタルツインがあります。
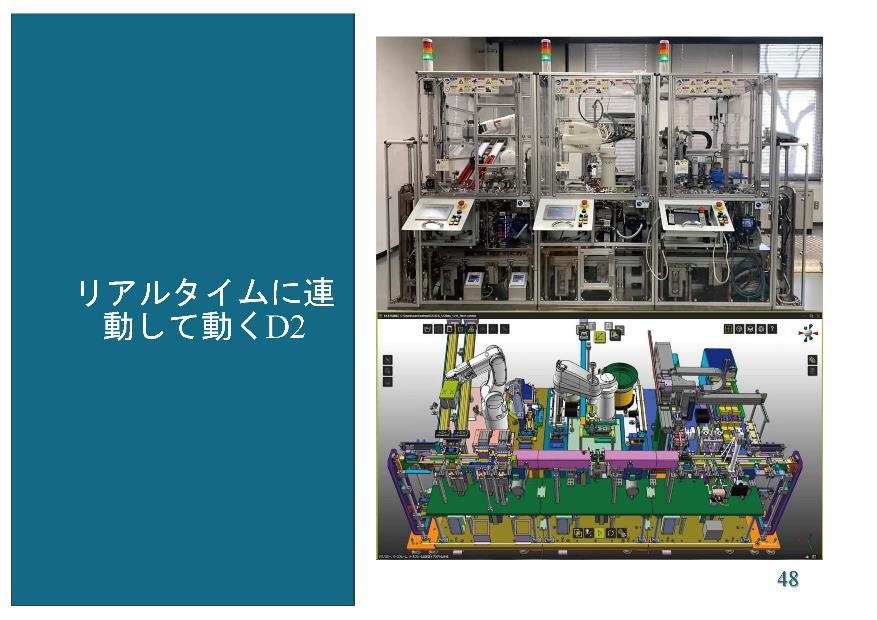
例えば、複数の熟練者にカイゼン作業をしてもらい、そのプロセスを学生が細かく記録していきます。そして記録の中から共通する作業プロセスを抽出するのです。
汎化プロセスモデルができあがると、今度は生産システムに詳しくない学生が、汎化プロセスモデルを見ながらプロセスの改善案を挙げていきます。4人の学生で実験したところ、汎化プロセスモデルを見たグループだけが問題点の原因を突き止められました。出された改善案は十分でないものの、それでも熟練者の改善案と共通性が高いことが分かりました。このような形で、作業プロセスを熟練者から初心者に引き継げるようになるものと期待しています。
熟練者の暗黙知を計算機上で形式知化しようとする試みは、これまで数多く行われてきました。しかし、シンボルグラウンディング問題が立ちはだかり、なかなかうまくいきませんでした。シンボルグラウンディング問題とは、例えば「速く」「ゆっくり」といった記述では、素人が見たとき具体的に何を意味しているのかが分からないという問題です。
ところが、これからはエンジニアの作業がデジタルツイン上で行われるため、サイバー上で見たデータやソフトウェアの操作はログとして記録可能です。そうすると、考えたことと実際の作業がどのように対応づけられたのかが分かるため、データやソフトウェアの操作としてグラウンディングできるようになったのです。
今後は、自動化できるタスクから逐次自動化(ソフト化、AI化)を進めていき、人の判断が必要なタスクと混在させたプロセスを記述できる状態を目指します。うまくいけば、「文脈」までも記述できるようになるかもしれません。
<対談>なぜ日本のDXはなかなか先へ進めないのか
引き続いて、佐野、勝見、梅田教授の話を受けて、聴講者の意見も交えながらディスカッションが行われました。
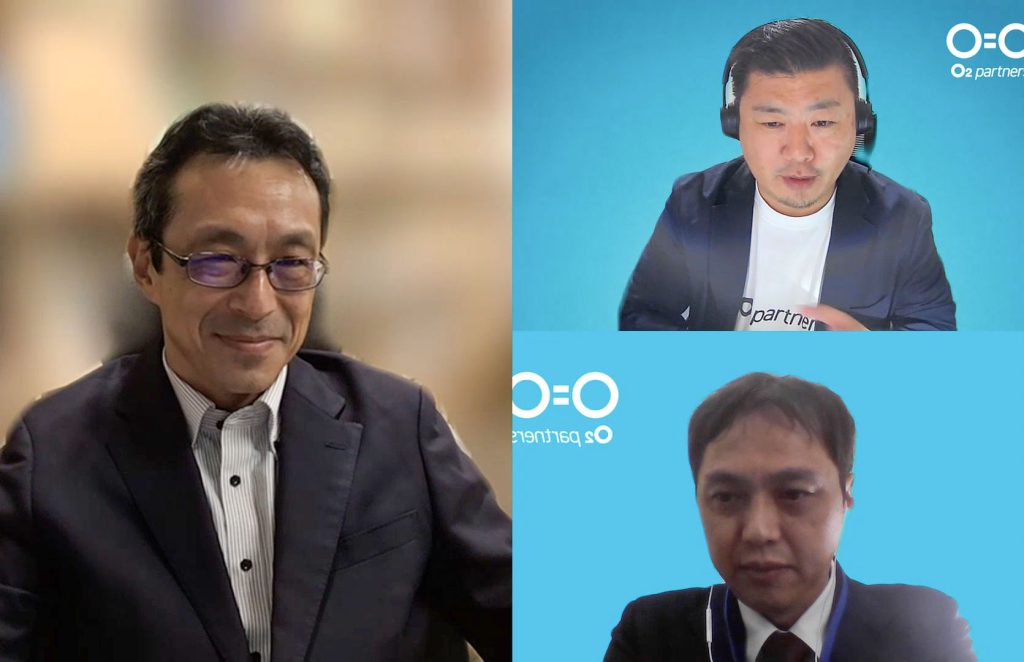
ボトムアップ型の日本で求められる「腹落ち感」
勝見:日本企業はアメリカや中国の企業とは違って、トップダウンでものごとを決めていくことがあまりないですよね。もちろん強力なリーダーシップを持っていて、「右向け」と言えば、みんなが右を向き、世界で戦っている会社もあります。一方で、日本を代表するような企業であっても、納得できなければ右を向かない会社もあります。それは言うこと聞かないのではなく、「腹落ち感」で動いているからであって、これはとても大切なことだと思います。
梅田:そうですね。
勝見:モノ作りに携わる現場の方も、ミドルマネジメントの方も、みなさんボヤッと仕事することなんてなくて、考えて考えて、考え抜いた最適解の上を進まれています。それが時間とともに積み重なって、ノウハウやベテランの技術になっているのかもしれません。そうした方たちが納得する施策が出てこないから、なかなかDXが進まないのではないでしょうか。これは恐らく、日本という国ではずっと変わらないように思います。また、強力なリーダーシップを持った会社ばかりになることもないでしょう。
現場が腹落ち感を持てて、しかも自身の持つ価値を発揮できる道の上を進むのが、日本的なDXなのではないでしょうか。
梅田:現場の人たちは、デジタル化してしまうと何か大事なものを失ってしまうような感覚があるのかもしれません。デジタル・トリプレットは、その何か大事な部分をすくい上げて、よりよくしながらデジタル化するものだということをお伝えしたいですね。
なぜ日本はデジタル競争力が低いのか
聴講者:デジタル競争力ランキングで適応力や変革力の評点が低いことは、良い面と悪い面、どちらもあると考えます。良い面で言えば、日本ほど長寿企業が多い国はありません。現在における問題点は、単に変革力の評価が低いことではなく、結果が出るまで時間を要することを認識して、長期に取り組むことをせず、近視眼的、短期的に利益が出ないから現業を現在のやり方で続ける以外にやりようがなかった結果として、変革力の評点が低い点にあると考えますが、いかがでしょうか。
勝見:本当におっしゃる通りですね。四半期決算もそうですが、大企業を中心に早く結果を出さないと納得してもらえない状況でデジタル化し生産性を上げなければならず、そのROIも常に求められています。長い時間をかけた変革が難しくなっていますよね。先ほど「腹落ち感」の話をしましたが、何かを変えようとしたとき、だんだんと階層的に浸透させていくような意思決定やプロセスも必要だと思います。
また、ダイバーシティによってさまざまアイデアが集まるようになっていますが、その企業としてかくあるべしというルールに基づくと、どうしてもイレギュラーになってしまって、スピード感を持って適用できないという状況もあるでしょう。
梅田:じっくり時間をかけて根本的に問題を解決するのは、非常に重要ですよね。それが理想論だと思う反面、アメリカやヨーロッパだとスピード競争をグローバルスタンダードとして仕掛けてきます。それに合わせているうちに、自分たちのペースを見失ってしまうことはあります。
日本は前例主義の方が多いので、何もしないのに時間が経ってしまうことがあります。また、時間をかけて本質的な変革をすべきかどうかを見分けることも難しいのではないでしょうか。
勝見:挑戦することのハードルがすごく高いのかもしれません。挑戦してもいいけど、失敗するなというプレッシャーもありそうです。
そうは言っても、挑戦する場を与えてもらいながら育った方もたくさんいらっしゃいます。それが昔よりも難しくなっているのかもしれないですね。
変革の費用対効果を測る指標を見直してみる
勝見:製造業でエンジニアの経験がある佐野さんはいかがですか。
佐野:変革の費用対効果をどう捉えるかで、進みやすさが違ってくるのではないでしょうか。ちょうどご支援しているお客さまも同じようなことをおっしゃっていて、一旦、効果をお金に換算するのをやめてみようという話をしています。
変革によって何時間減るのか、その結果いくら削減できるかを天秤にかけて判断するのも大事だとは思いますが、一方でデジタル化は費用対効果だけが目的とは限りません。
例えばデジタル化度合いや、ルーチンワークの割合といった、違う軸の指標を設定してみてはどうでしょう。それによって、変革の時間をうまく作ることができるかもしれません。製造業はお金の面で几帳面に効果を算定しますが、少し視点をずらしてみると、変革を進めやすくなるところもあるのではないでしょうか。
梅田:本当は付加価値アップのためのデジタル化なのに、日本のデジタル化はコストダウンばかりだと指摘する識者がいました。その話と通じますね。
佐野:工数をお金に換算していかに効率化するかというのは大事ですが、さらに先の改革を描いていくときには、なかなか簡単にはお金に換算できません。両方の視点が必要だと思います。
梅田:大企業のリスク管理では難しいのかもしれませんね。佐野さんから「スタートアップ企業は、有名企業があまり持っていない資産、すなわち厳格なプロセスが必要なために扱いにくい資産を持っている場合がある」という話がありました。
佐野:Infineonの考え方ですね。
梅田:ドイツの大企業でも、硬直性みたいなものがありますよね。
佐野:そうですね。訪問時には、そういう話も出ました。ゆえに、自分たちの中でできることでも、あえて外へも出して任せてみて、限定的に口を挟みながら進めているとおっしゃっていました。
大企業は力があるし、優秀な方もたくさんいらっしゃるので、あえて外に任せてみるのは非常に勇気あることだと思います。でも、それを必要な取り組みだと理解しているのです。
ハブとなる企業に期待される役割
梅田:日本企業でもスタートアップと組むことが増えていますか。
勝見:コロナ禍の前ですが、大企業が過去最高の内部留保を蓄えて新規事業開発に取り組んでいた頃、自社の技術を使って事業を広げるだけでなく、スタートアップへのCVC投資が非常に盛んでした。今はスタートアップとの連携が安定的に続いています。大企業が出資を含めてスタートアップと協力する機会は、10年前に比べるとずいぶん増えてきている印象です。
一方で、出資や資本業務提携をしながらも、お互いのスピード感やロジックが違うところもあって、うまくインテグレーションが起きないという話も聞きます。
佐野:大企業のみなさん、いろいろと新しいスタートアップや新しい技術を探索していて、積極的にコミュニケーションをとっているようです。
ただ、いざ新しい技術が見つかったとき、それを自分たちの製品やサービスにどう組み込むのかを実証する段階にきて、それをどちらが担うのかでスタックしてしまうことが結構あります。スタートアップには、そこまで担うリソースがない。一方で大企業は、大企業とはいえども技術者のリソースを回すのが難しい。
そこをブレイクスルーするためにも、ハブになる企業が必要なのだと思います。我々がお手伝いした例もございます。
大企業がデジタル・トリプレットに取り組むモチベーション
勝見:先生の研究室では、大企業と研究者が一緒に取り組みを進めているわけですが、大企業の姿勢や意気込みは、アカデミック側からはどのように映っていますか。
梅田:私たちがお付き合いしているのは、変革力が高い企業が多いと思います。問題意識はかなり共通していて、「デジタルを入れなきゃいけない」、「技術者の高齢化で生産の質を保てないのでは」といった危機感が強いですね。
デジタル・トリプレットを現場に入れるのはハードルが高いので、フラウンホーファーのような実用化研究を担ってくれる存在があれば助かります。フラウンホーファーは、わりと泥臭いことを厭わずにやってくれる印象です。
勝見:泥臭いことをしっかりやらないと前に進みませんが、それを是としてくれず、早く結果を求められているような気もします。モノづくりのことをよく知っている方からすると、そんなに簡単ではないのに、と言いたいでしょうね。
熟練者の「当たり前」をどのように引き出すか
勝見:ベテランの熟練者が退職を迎え、引き継ぎのためにいろいろ書き残してくれたので何とかなるだろうと考えていたら、翌週からトラブルが頻発したという話を聞きました。熟練者は普段かなり細かい配慮をしていても、それはいちいち書き残すほどじゃないと考えていたのですが、そうしたことの積み重ねが高品質のモノづくりを支えていたわけです。
そういうものを、すべて吸い上げながら形にしていかないと、今以上に大変になってしまうでしょう。競争力どころか、モノづくりそのものが危ぶまれます。
佐野:数年前、ドイツの企業で技術者の技能を伝承するプロジェクトに携わりましたが、ドイツでもそれほど上手に伝承できているわけではないのだと感じました。
梅田:先ほど勝見さんから、熟練者にとっては当たり前すぎることが多いという話がありました。私たちは熟練者にヒアリングするわけですが、あまりにも常識的すぎて大事なことが書き残されないことがあります。
勝見:当たり前のことは、人によって全然違います。伝承していくには重要なところを漏らさず紡いでいくことが大事なのですが、その塩梅がなかなか分からない。自社の中だけだと分からないかもしれないし、世代によって当たり前ということもありますし、難しいですね。
梅田:世代が違う人や少し専門分野がずれている人、他社の人など相対化する工夫が効いてくるのではないでしょうか。私たちの研究では、熟練者と素人の関係でやってみているところです。
勝見:弊社のコンサルティングでは、暗黙知を可視化していきます。弊社のメンバーはほとんどが元エンジニアなのですが、自分がいた業界や作っていた製品が関係する方にヒアリングすることは、ほとんどありません。必要なのは工学の基礎的な知見や教科書レベルの共通項です。違う業界の視点から見て初めて浮き彫りになってくることがあります。同じようなものを作っていたコンサルタントが聞いたのでは、お互いが放置してしまうことがある。一方で完全な素人が聞いたのでは、聞かれる方が嫌になってきます。
佐野:私はもともと半導体の製造装置を設計開発していたので、弊社で半導体や装置に関する仕事には、ほとんど関わってきませんでした。ただ、最近は半導体や装置を見たときに違う見方ができるようになったので、そろそろ装置もいいかなと思いだしました。
勝見:最後に、今日の総括をお願いします。
佐野:決してドイツが最先端だということではないし、ドイツについていかなければならないわけでもない。一方で自分たちの遅れを認識して、何とかしようと着実な動きを産官学で進めていることは参考にしていいのではないでしょうか。そのような場を一緒に作っていければ、より日本の製造業が面白くなると思いました。
梅田:佐野さんにドイツの最新状況を伺って、必ずしも進んでいないし、66%が遅れを感じているというのが印象的でした。ただし、ドイツは新しい方向性を2011年から言い続けてきました。その点は見習わなければいけないと思います。
今日は、変革に向けたいろんなヒントをいただけました。