設計シミュレーション活用の落とし穴
- テクノロジー
- コンサルティング
- 製造業
- ものづくり
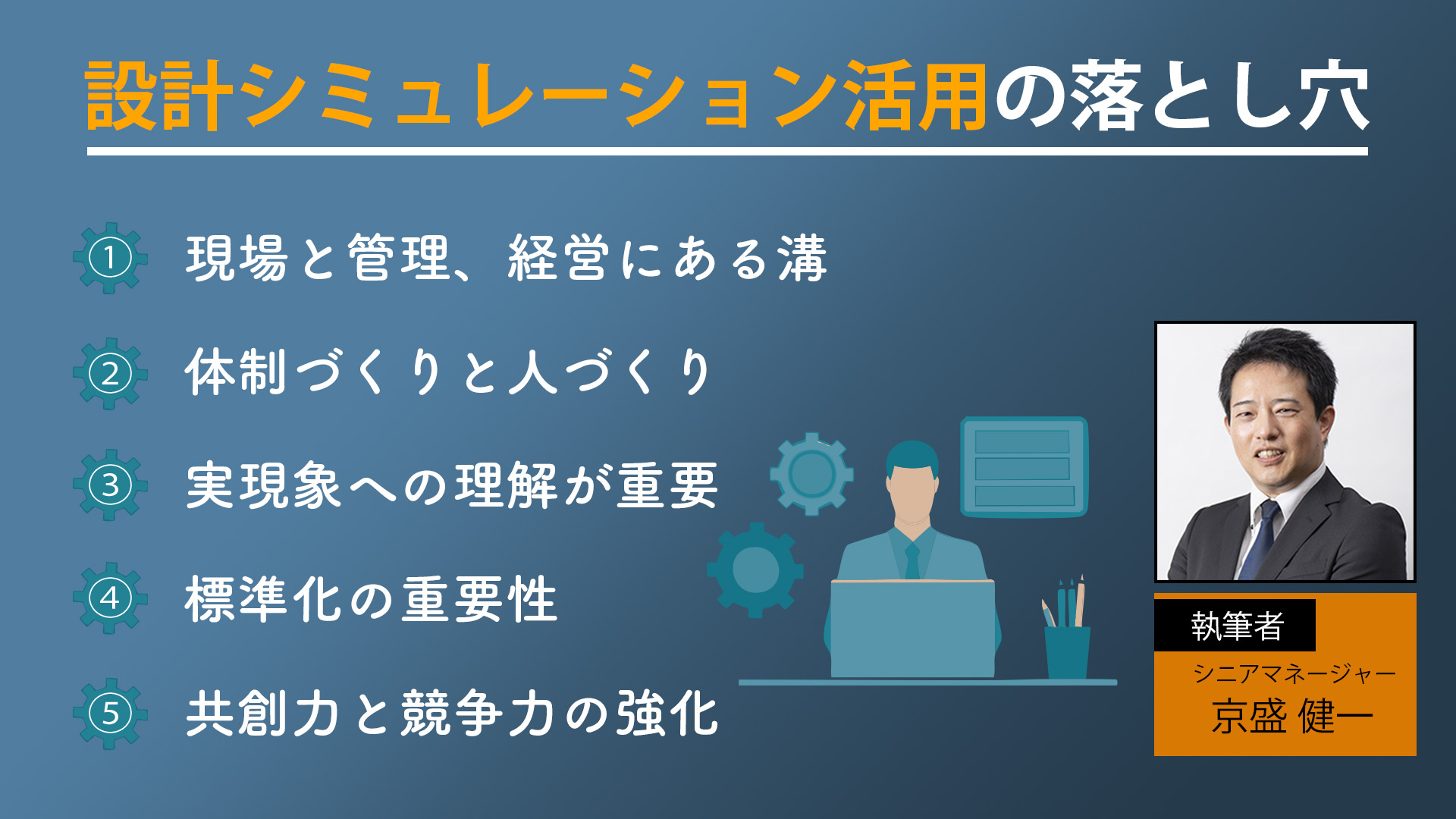
目次
はじめに
筆者は長年にわたり、ITベンダー、製造業コンサルタントの立場として、多くの企業におけるシミュレーション活用支援を行ってきた。多くの企業がシミュレーション技術を導入して現場で利用しているものの、導入当初の期待とは異なり、思っていたような成果が十分に獲得できていないと考えているマネージャーや経営者の方が多いのが現状である。期待と現実の間にある落とし穴には幾つかのパターンがあるように思う。そこで全5回の寄稿では、どのような落とし穴があるか紐解いてゆきたい。
1 現場と管理、経営にある溝
シミュレーション活用に向けた取組の実態
開発設計業務においてシミュレーション技術を活用して業務改善や変革を進めてゆく際には「①ソフトウェア&ハードウェアの導入」だけでなく、自社製品の開発対象の特性に応じた「②シミュレーション技術の確立」に必要となる施策を実行した上で、設計課題をなるべく設計初期段階から早期に潰し込めるよう「③シミュレーション活用を前提とした設計プロセスの改革」が必要である。
筆者の経験から①については多くの企業で十分な対応がなされているかと思う。②については、シミュレーション技術に関する高い見識を有する方が社内に存在するかに大きく依存している。社内に不在の場合は、外部有識者のサポートを受けるケースもあるが、残念ながら②の重要性に気づいていない企業も一定数存在している。その中には設計者向けツールを購入する際に「誰でも簡単にシミュレーション出来ますよ」という謳い文句を鵜呑みにして導入しているケースも少なからずある。③について実現できている企業が少ないのが現状であり、設計プロセス改革をリーディングする旗振り役がいないのが原因ではないかと考えている。
目的と課題の明確化と議論が必要
シミュレーション活用に向けた取組が期待通りに進んでいない原因は何か?活用を推進できる対応できる人材が少なく、そのため必要となる活用施策を十分に実行できない、成果がでないため活動が縮小されてしまう、そのような悪循環に陥っている企業が多いように感じる。サポートを通じて接してきた有識者の方々からは、シミュレーション活用の重要性を十分に理解しているマネージャーや経営者が少ないといった話もよく聞かれる。一方でマネージャーや経営者の立場からすれば、投資に対する効果が見えにくいと言った意見もよく聞かれる。
このような現場と管理、経営にある溝を埋めるためにはどうしたら良いか?現場と管理、経営の異なる視点から、シミュレーション活用の目的と課題を明確化した上で議論し、中長期的な実行施策と計画を考えてゆく。そこから始める必要があるのではないかと考える。
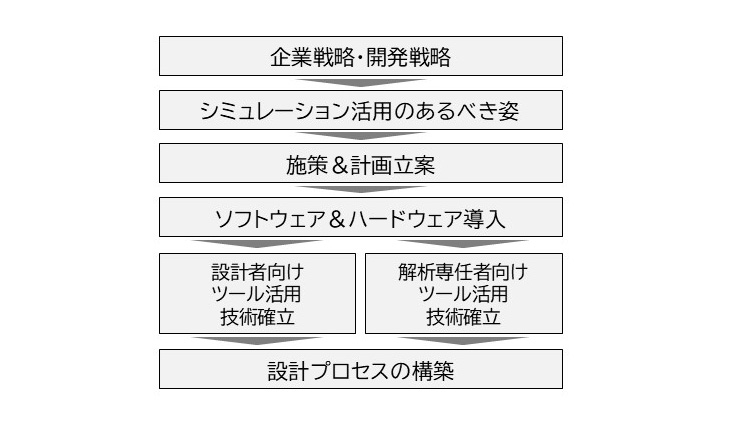
2 体制づくりと人づくり
シミュレーション技術は諸刃の剣
シミュレーション技術の扱いの難しさを「諸刃の剣」と表現するコメントを聞いた時、いい得て妙だと思ったことがある。上手に使えば恩恵を得られるが、特性を十分に理解せずに誤った使い方をしてしまうと、損失を引き起こしてしまう危うさを持ち合わせているということを意味する。
これはソフトウェアに問題があるのではなく、あくまで利用者側の問題である。ハードウェアやソフトウェアの進歩によって、誰もが比較的簡単に結果を得られるようになったが、条件設定、要素分割、アルゴリズムが適切に選択されないと正しい解が得られない。以前に比べてオペレーションが容易になり、アルゴリズム自動選択機能などのシステムによる利用者サポート機能は拡充されているが、本質的には利用者側に一定のスキルと見識が求められる技術である。
エキスパート人材の必要性
妥当な解を得て妥当な評価をするためには、具体的にどのような技術が必要か?その要件と必要な力量を理解するための1つの有効な手段として、一般社団法人日本機械学会にて2003年より開始した「計算力学技術者資格認定」がある。解析専任者や設計者による解析を推進する立場の方は資格を有している事が好ましい。社内で実施されるシミュレーションの結果品質を確保するため、取引先に解析結果の説明をする際に信頼度を上げるため、座学教育やOJTを通じた活用人材育成のために不可欠な存在であると言える。また、自社のシミュレーション活用のあるべき姿の立案、技術構築に向けた実行計画の立案など、シミュレーション活用による事業貢献を実現するための引率を担う役回りだと言える。
体制検討の議論が必要
エキスパート人材は十分に役割を果たせているのだろうか?そこに理想と現実のギャップがあると筆者は考えている。自社のシミュレーション活用の運用や体制が十分ではないと考えているエキスパートが多いではないかと思う。
取組が上手く進んでいる、成果が上がっている企業では、開発設計の技術管理部門と解析専任チームが連携し、開発設計業務プロセスにおけるシミュレーション活用を前提とした役割分担が上手く機能している。職務分掌を定義してそれぞれの役割をしっかり担う事は当たり前の事ではあるが、ことシミュレーションの業務運用に関わる組織統制、体制のあり方については、マネージャーや経営層の理解が十分でないのではと思う。経営層に理解頂くには、先行企業の事例・進め方を参考にするのも有効である。外部有識者から先行企業での進め方を聞き、自社の取組と体制の足らざる部分を明確にした上で、職務分掌の整理、見直しをしてみるのが良いのではないだろうか。
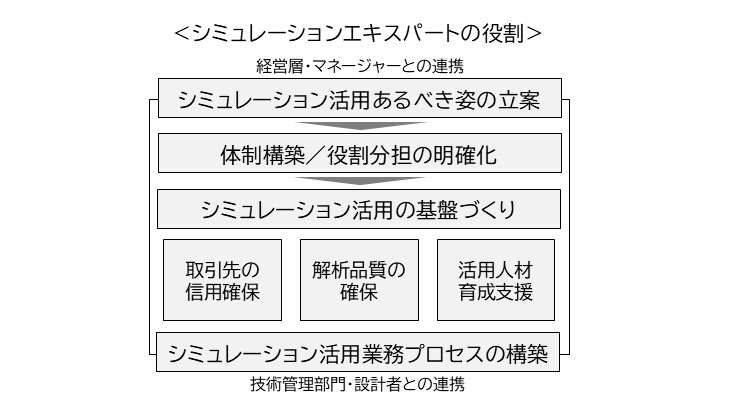
3 実現象への理解が重要
シミュレーション結果の評価
一般的にシミュレーション結果と実機試験結果には差が生じるため、それぞれの結果を比較して相関係数を求めておき、新たなシミュレーション結果を得た際には、その値に相関係数を乗じて実機試験の結果を推定する。しかしながら、相関係数の取り扱いを間違っているケースは少なくない。相関が低い場合は、シミュレーション結果に相関係数を掛けた値の信用度は落ちるため、バラツキを考慮した評価のテクニックが必要である。また、なるべく高い相関が得られるよう、シミュレーションと実機試験、それぞれにあるバラツキを抑制してゆくための改善が必要である。相関を阻害する要因として、具体的にどのようなものがあるのだろうか。
バラツキの要因と抑制
シミュレーション結果のバラツキは、メッシュサイズやメッシュタイプ、境界条件の設定方法やアルゴリズム、結果処理方法によって生じる。シミュレーションモデル作成の標準ルールを定め、これに準拠した運用をする事で、ある程度バラツキを抑制することが出来る。
実機試験結果のバラツキ要因については多岐にわたる。プラスチック製品の場合、薄肉やヒケがあったりソリやウネリもある。材料内部には空隙やウェルドのミクロな不具合、繊維配向や結晶化度分布に個体差がある場合もある。アセンブリ状態であれば、部品間の位置やクリアランスも個体差がある可能性がある。また、試験体の設置位置のズレ、試験環境の温湿度の影響を受ける場合もある。これらのバラツキは抑制できるものもあるが、その多くは抑制ができない。どのような対策をすれば良いだろうか。
実機のバラツキ要因の把握
3次元形状測定器やX線CTなどの計測技術と、点群データを可視化し、そこからデジタル空間上で寸法を計測する技術の発達により、実機のバラツキの程度を把握することが容易になってきた。これらを用いて、先述のような形状や材質のバラツキの程度が把握でき、相関阻害要因の特定やその程度を把握する事が出来る。また、測定結果から解析用モデルを作成することも出来るため、スキャンモデルを強度解析や振動解析に取り込み、よりリアルなシミュレーションを行うことも可能である。
これらの取組は、相関阻害要因を把握して、シミュレーション結果に対する考察力を高めるだけではなく、様々なバラツキがあっても、要件をクリアできるようなロバストな設計をするためには、どうしたら良いかの検討材料を得ることにも繋がる。一度、自社の製品のバラツキがどの程度なのか、調べてみるのは如何だろうか。
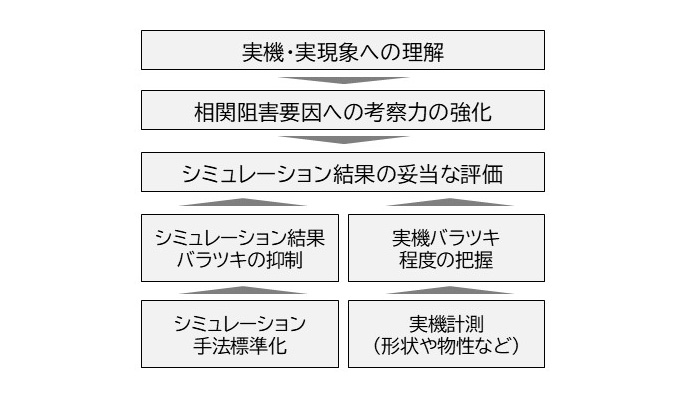
4 標準化の重要性
シミュレーションに纏わるヒヤリハット
筆者はシミュレーション活用の現場支援において、幾つかのヒヤリハットに遭遇している。印象に残っているのは、実機試験にて強度不足が確認されたため、対策形状を検討した上で、シミュレーションにて変更前後の最大応力値の比較を行ったという事案である。担当者は対策により最大応力値が低下すると期待したが、対策形状の応力値が高かったため、メッシュサイズを変更して値を下げ、その結果を取引先に説明しようとしていた。
モデルを確認した結果、部品の固定面の境界条件の設定に誤りがあることが判明、境界条件の見直し行い、対策前後の両モデルを同一のメッシュサイズで再計算し、妥当な対策有効性の評価が行えたので事なきを得た。
結果品質が個人任せ
もし仮に誤った結果を提示して、先方担当者から境界条件やメッシュサイズが妥当か指摘を受け事実が判明すると、技術レベルが低いと判断されるだけでなく、意図的に情報操作を行ったと誤解されかねない。倫理的に問題ありと受け止められてしまうと、企業間の信頼関係に悪影響を及ぼしかねない。これは担当者の問題ではなく、会社全体の問題として受け止めるべきである。シミュレーションの品質コントロールが担当者任せになっており、担当者のKKDH(経験と勘と度胸とハッタリ)が横行している状態といえる。シミュレーション品質に対する統制機能を強化してゆく必要がある。
そこで参考にしたいのが、日本計算工学会標準である。工学シミュレーションの品質保証における基本的な要求事項、それを実装した標準手順がまとめられた内容であり、品質保証を行う仕組みの構築、改善活動を行ってゆくための指針となる。ご存知の方も、今一度標準をご覧頂くことを推奨する。
設計とシミュレーションの標準化
シミュレーションプロセスの標準化は、シミュレーション品質保証の観点から非常に重要な取組であるとともに、設計品質の向上、更には開発設計リードタイムの短縮に寄与することが出来る。標準に準拠したプロセスで得たシミュレーション結果は相対比較が可能となり、変更対策による効果確認の妥当性が確保される。
また、設計標準のルールも統一されていると効果がより大きくなる。設計標準とシミュレーション標準に準拠したシミュレーション結果が蓄積され共有されることで、設計案検討において試行錯誤に要する時間の短縮、試作回数の低減、また評価項目の集約を実現することも可能になってくる。
設計標準とシミュレーション標準を組み合わせることで、開発設計のリードタイム短縮と設計品質の向上に貢献が出来る。自社におけるそれぞれの標準化の取組の現状を確認しては如何だろうか。
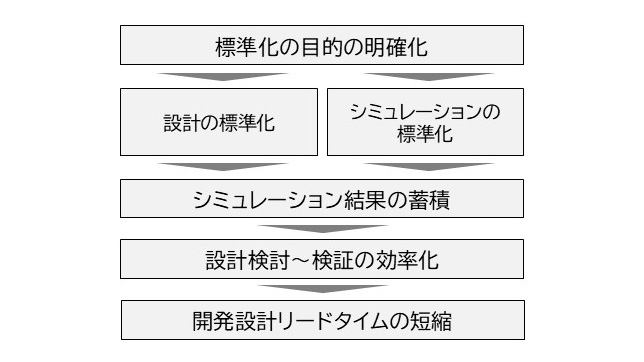
5 共創力と競争力の強化
シミュレーションを活用し倒す
多くのシミュレーション活用の現場では、解析から得られた結果に対して、判定基準に基づいたOK、NGの評価が行われている。判定がNGだった場合、その結果からどこに設計上の問題点があるかを読み解き、考察をしながら対策検討を行ってゆく。しかしながら判定がOKだった場合、設計的になぜOKだったのか、改善代は無いのかといった考察は、前者に比べると実施されていない現場が多かったように思う。
これはシミュレーションを行う事の価値を十分に引き出せていない状況だと言える。利用者がシミュレーションを試験代替手段として捉えており、最適な設計案を導き出すためのツールだと認識して使っていない、また、そのような教育を受けていない場合が多い。
シミュレーションがもたらす価値
実機による強度試験の場合、指定荷重で破損しない事を確認できれば良く、応力分布を可視化するための装置を併用したり、事後の試験体の変形挙動や材料の変質、微細な破損が無いかの確認まで行われるケースは限られる。当然コストと手間がかかる。しかしながら、シミュレーションであれば、例えば応力値の結果を一つとっても、応力集中箇所の最大値だけでなく、全体の応力分布やその勾配が可視化され、圧縮応力なのか引張応力かも分かる。また、全体的な変形と局所的な変形のモードと合わせて考察することで、強度・剛性と形状の関係性を読み取ることが出来る。
形状が持つ意味を考えながら適宜シミュレーションを行うことで、その形状がどのような機能を果たすのか、他の部位や全体とのバランスは最適なのか考えを巡らせる。この一連の思考プロセスが設計ノウハウそのものになり、その検討過程と結果を形式知として共有することで、社内全体の設計力を高めてゆくことが出来る。
さいごに
筆者が長年にわたってITベンダー、製造業コンサルタントの立場として、多くの企業におけるシミュレーション活用支援を行ってきた経験を通じて、開発設計業務においてシミュレーション技術を活用して業務改善や変革を進めてゆくための課題、必要となる取組や考え方を挙げさせて頂いた。
設計者がシミュレーションを活用して可視化された情報を基に設計案を詰めてゆき、その結果を基に関係者とコミュニケーションを図りながら、より高度な設計案になるよう改善を重ねてゆくことで、企業内での共創力とライバル企業に対する競争力を高め、更には日本の製造業全体の優位性を高めてゆくことが出来るのではないかと筆者は考えている。今回の寄稿を通じて、シミュレーション活用に対する関心が高まる一助になれば幸いである。
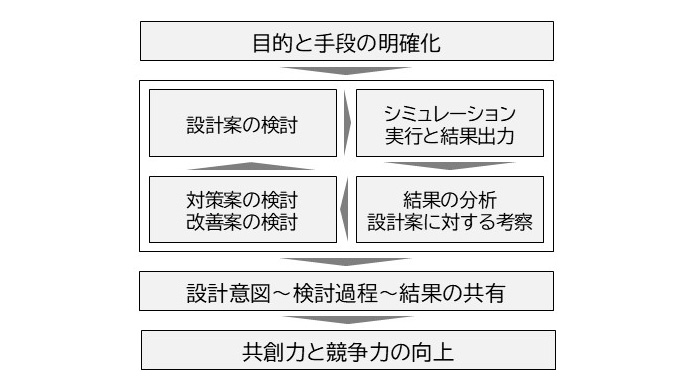