DXではなく“XD” ~再び世界で輝くために
- テクノロジー
- コンサルティング
- 製造業
- ものづくり
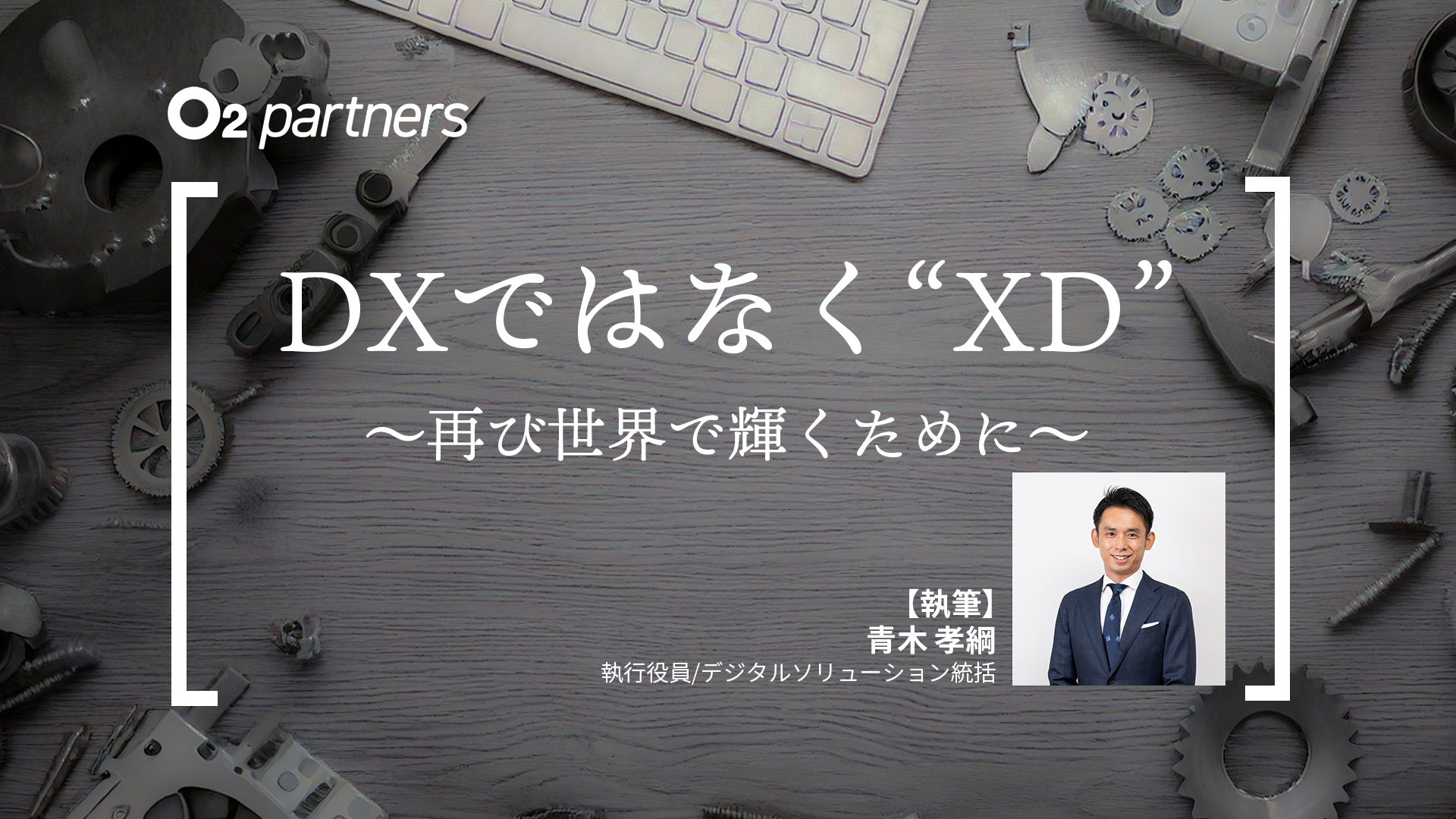
目次
1 低迷する労働生産性
デジタル化は新価値創造の基盤
製造業における日本の労働生産性は、かつて世界の上位に位置していた。しかし、この30年で順位を大きく下げ、主要国の中でも低迷を続けている。この現状は、国際経営開発研究所(IMD)の世界競争力ランキングにも如実に表れている。65カ国中、「ビジネスの効率性」の総合順位は51位と低迷し、特に「生産性と効率性」および「人事・組織の管理」の分野での評価は著しく低い。
なぜ、このような事態に陥ってしまったのか。その本質的な要因は、デジタル化に対する誤った理解と取り組み方にある。
2007年の米国大統領経済報告は、重要な指摘をしている。情報・通信機器やソフトウェアの導入という単なるIT化だけでは、生産性の向上は実現できない。真の生産性向上には、人材育成、組織改革、業務プロセス改革などと一体となったデジタル化が不可欠だというのだ。
しかし、日本の多くの製造企業では、この本質を見誤ってきた。デジタル技術を活用した抜本的な業務改革ではなく、既存の業務プロセスの一部をIT化する取り組みに終始してきたのである。その結果、投資は表面的なシステム導入に留まり、真の意味での生産性向上には結びついていない。
さらに深刻な問題は、デジタル化投資の判断基準にある。日本の製造業では、投資の是非を「人件費削減効果」で判断する傾向が強い。しかし、日本の労働コストは国際的に見て比較的低水準にあるため、この基準では大規模なデジタル化投資の正当化が困難となる。
この状況は、負のスパイラルを生んでいる。デジタル化投資が進まない結果、企業は人的努力に依存したカイゼン活動に注力する。それによって業務プロセスはますます人依存となり、デジタル技術の導入はさらに困難になっていく。このサイクルが、日本の製造業の労働生産性を長期にわたって停滞させている根本的な要因となっていると捉えている。
しかし、まさに今こそが変革の好機である。エキスパートやエースと呼ばれる人達が持つ知見や判断の根拠が現場に残る今だからこそ、それらを生成AI等のデジタル技術で効果的に継承・展開できる。人が過剰に介在する業務から脱却し、人とデジタル技術が最適に協調する新たな製品開発プロセスを構築する。それが、日本の製造業が再び世界で競争力を獲得するための必須条件となっている。
製造業のデジタル化は、単なる省人化や効率化の手段ではない。それは、人の創造性や専門性を最大限に引き出し、新たな価値創造を可能にする基盤である。この後はこの視点に立った具体的なデジタル化の在り方について、詳しく述べていきたい。
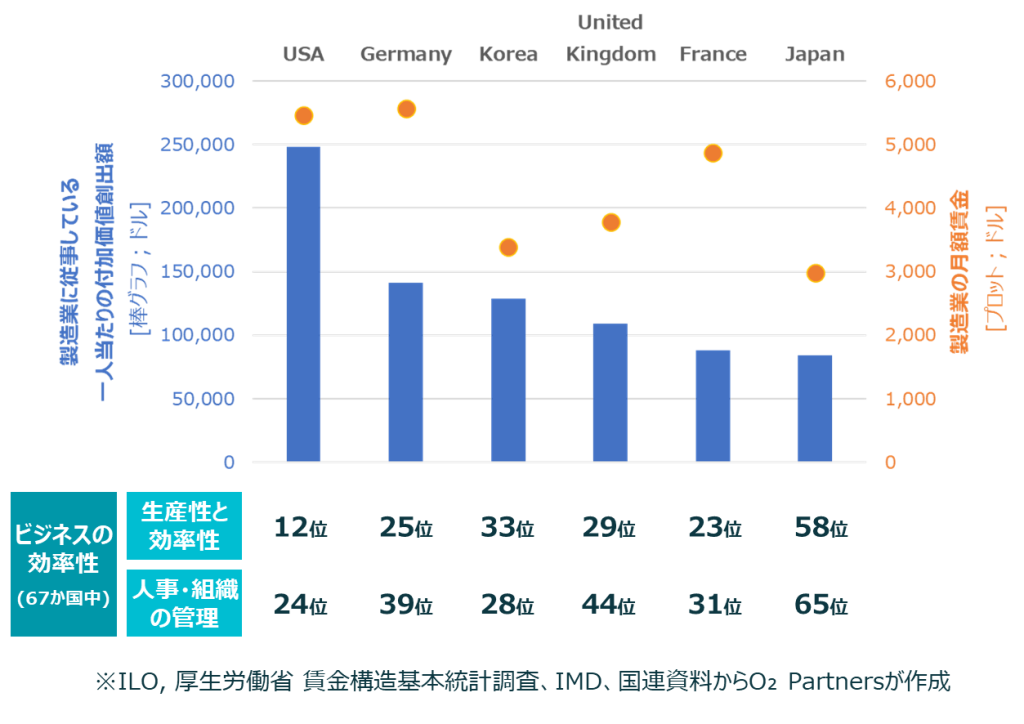
2 ドイツの支援に学ぶ
業務工程 全体見直しを
日本と同様、ドイツの企業も当初はDXの進め方に悩んでいた。「DXすべき」という漠然とした焦り、「何から始めればよいかわからない」という戸惑い、さらには「過去のDX失敗経験」など、現在の日本企業が抱える課題と同じ悩みを抱えていた。
しかし、ドイツが日本と大きく異なるのは、これらの課題に対する国としての支援の在り方である。
ドイツでは、全国各地に設置された中小企業デジタルセンターを中心に、企業のDX推進を無償で支援する体制を構築している。さらに、フラウンホーファー研究所など、産業界の技術革新を支える研究機関とも緊密に連携している。これらの機関は、プロバイダー中立の立場をとりつつ、企業のDX戦略立案から業務プロセス改革までを一貫して支援する。
特筆すべきは、この支援体制が単なる補助金給付ではなく、「全体最適を見据えたデジタル化戦略の策定」を重視している点だ。まず企業の現状把握とありたい姿の明確化を行い、そこから逆算して必要な施策の優先順位付けを支援する。その結果、場当たり的なシステム導入や、部門個別最適に陥ることを防いでいる。
この取り組みの成果は数字にも表れている。政府の支援施策により、投入された助成金の2.5倍のデジタル投資が誘発され、支援を受けた企業の売上高は3.3倍に増加した。さらに、その効果は取引先企業や業界全体にも波及し、産業界全体のデジタル化を加速させている。
対照的に、日本の支援は都道府県単位での取り組みが中心で、補助金による金銭的支援が主である。確かに資金面での支援も重要だが、より本質的に必要なのは、企業が抱える「どう進めればよいのか」という悩みに寄り添い、実践的な道筋を示すことだ。さらに重要なのは、道筋(=戦略)を描いて終わりではなく、その実践支援をとおして企業自身の変革力を培っていくことである。
ここで注目すべきは、ドイツの支援機関が「デジタル化ありき」のアプローチを取っていない点だ。彼らが重視するのは、まず業務プロセス全体を見直し、その上で必要なデジタル技術を選定・導入していく方法である。つまり、デジタル化は目的ではなく、業務改革を実現するための手段として位置づけられているのだ。
日本企業の多くは、既存の業務プロセスを前提に、その一部をIT化する取り組みに終始してきた。しかし、真の競争力強化には、業務プロセス自体の抜本的な見直しが不可欠である。その上で、見直された業務プロセスを効果的に支援するためのデジタル技術の活用を考えるべきだ。
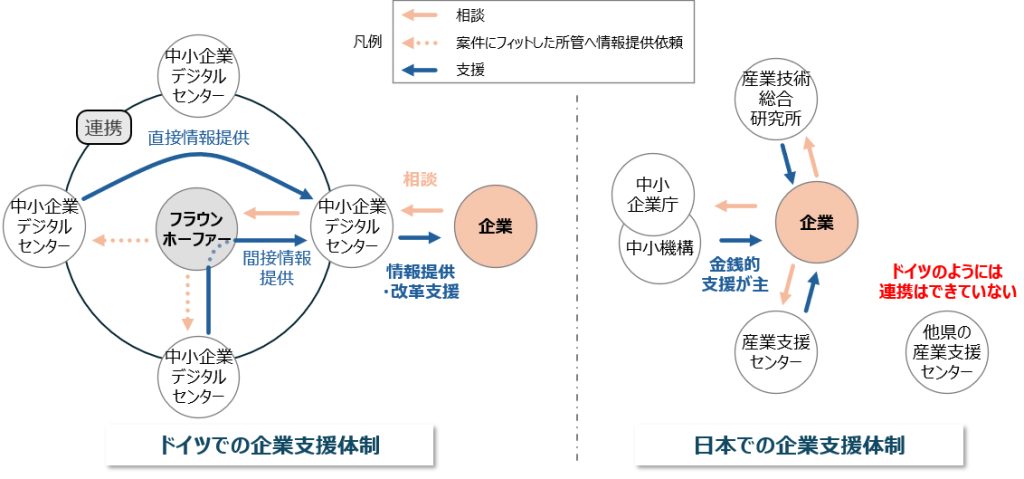
3 真の競争力強化
将来像から逆算し推進
前回、ドイツの事例から、デジタル化を目的化せず、業務改革を実現するための手段として位置づけることの重要性を述べた。今回は、そのような「X(業務改革)からD(デジタル技術の活用)へ」のアプローチ、すなわち”XD”を成功に導くための要諦について考察したい。
まず認識すべきは、真の競争力強化には業務プロセス自体の抜本的な見直しが不可欠という点だ。これまで多くの企業が、既存の業務プロセスを前提としたIT化によって改善を図ろうとしてきた。しかし、そのような取り組みでは、せいぜい既存プロセスの効率化に留まり、本質的な競争力強化には至らない。
では、抜本的な業務改革をどのように進めるべきか。成功事例から見えてくる重要なポイントは、経営層から現場まで、組織全体で同じ将来構想を語れているか否かだ。単なるスローガンや抽象的なビジョンではなく、具体的にどのような姿を目指すのか、その実現によって何が変わるのかを、組織の全階層で共有できていることが必要なのである。
ここで重要なのは、将来のありたい姿を描く際の視点だ。往々にして陥りがちなのは、既存の業務の流れを前提に、その効率化や最適化を考えることである。しかし、本当に必要なのは、「適切な情報を・適切なタイミングで・適切な相手に伝える」という観点から、業務プロセス全体を再定義することだ。
ここでいう「適切な情報」とは、単なるデータや結論だけではない。そこに至る思考のロジックや、検討結果とその導出根拠との関係性まで含めて、組織の共有知識として活用できる状態の情報を指す。このような情報の流れを起点に業務プロセスを再設計することで、真に価値を生む業務改革が可能となる。
さらに重要なのは、改革の「起点(現状)」と「到達点(ありたい姿)」を、関係者全員で明確に共有することだ。現状の課題とありたい姿を具体的に描き、それをステークホルダー全員が理解・納得していることが必要である。なぜなら、大規模な改革では必ず想定外の事態に直面するからだ。そのような状況でも、目指すべき到達点が明確であれば、その達成に向けた建設的な議論に集中できる。
このように、XDアプローチの本質は、デジタル技術の導入以前に、組織としての将来像と、それを実現するための業務プロセスの抜本的な見直しにある。その上で初めて、見直された業務プロセスを効果的に支援するためのデジタル技術の活用を検討すべきなのだ。
これは決して容易な取り組みではない。しかし、このような地に足の着いた改革なくして、真の競争力強化は望めない。デジタル化の波に押されるように進めるDXではなく、自社の将来像から逆算して進めるXD。それこそが、日本の製造業が今、最も必要としているアプローチなのである。
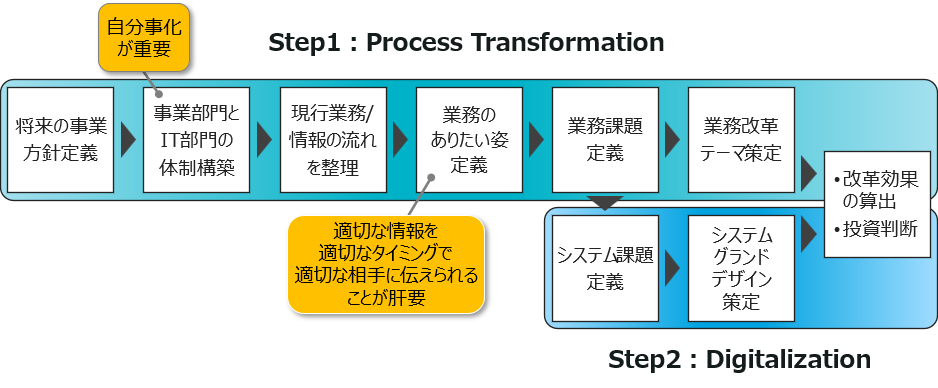
4 情報連携の設計
業務工程改革と一体推進
「事業判断に必要なデータを集めるのに人の手を介さないといけない」「設計変更の情報が製造現場に届くのが遅い」―。このような声は、製造業でよく見聞きする悩みではないだろうか。
これらの問題の多くは、組織の縦割り構造に起因する情報の分断に根ざしている。情報伝達の非効率性を詳しくみると、①情報の重複、②情報待ち、③過剰な情報処理、④不適切な情報伝達経路、⑤情報の不利用、⑥不要な情報移動、⑦情報の欠陥という7つのムダに分類できる。
これらのムダの解消には、個別の改善ではなく、業務プロセス全体の見直しが不可欠だ。例えば、ある工程の検討タイミングを前倒しにすれば、それに応じて必要な情報の詳細度や関連部署との情報共有のタイミングも変更が必要となる。つまり、情報連携の仕組みは、業務プロセス全体の中で捉え直す必要があるのだ。
例えば、構想設計から詳細設計へのスムーズな移行を考えてみよう。制御モデルやプラントモデルとE-BOMをどの段階でどう連携・反映させるべきか。設計変更や不具合発生時に影響範囲を迅速に特定するために、E/M-BOMとBOPの運用をどうすべきか。これらの答えは、組織が目指す「ありたい姿」によって変わってくる。
ある自動車部品メーカーでは、PLM導入の際、まず部門間の情報の流れを徹底的に分析した。その結果、設計変更の影響を受ける部品や工程を即座に特定できる仕組みを構築し、変更対応時間を従来の1/3に短縮することに成功した。これは、業務プロセスの見直しと情報連携の再設計を同時に行った好例と言える。
開発業務全般で生まれる情報を最大限活かすには、まず業務プロセスを整流化し、その上で情報の生成・連携・活用・管理をトータルで設計することが重要だ。その際のポイントは、人が介在する部分とデジタル技術を活用する部分のアーキテクチャを適切に設計できるかどうかにある。
例えば、設計者の試行錯誤のプロセスは人にしかできない重要な価値創造活動だ。一方で、その過程で生まれる検討結果や判断根拠の記録は、デジタル技術を活用して効率的に蓄積・共有できる。このように、人とデジタルの役割分担を明確にすることで、より効果的な情報連携が可能となる。
最後に一つ留意いただきたいのは、日本企業には「一度決めたことを長く続ける」という特徴があるが、XD改革においてはそれが逆効果になる可能性があるということだ。情報伝達の方法やデジタル技術の活用方法は、定期的に見直しを行う必要がある。なぜなら、ビジネス環境の変化とともに、より効率的な情報連携の方法や、より適切なデジタル技術が登場する可能性があるからだ。
真に効果的な情報連携を実現するためには、業務プロセスの見直しと情報連携の設計を一体で考え、それを継続的に改善していく姿勢が必要なのである。これこそが、XD改革がもたらす情報連携の本質的な変化と言えるだろう。
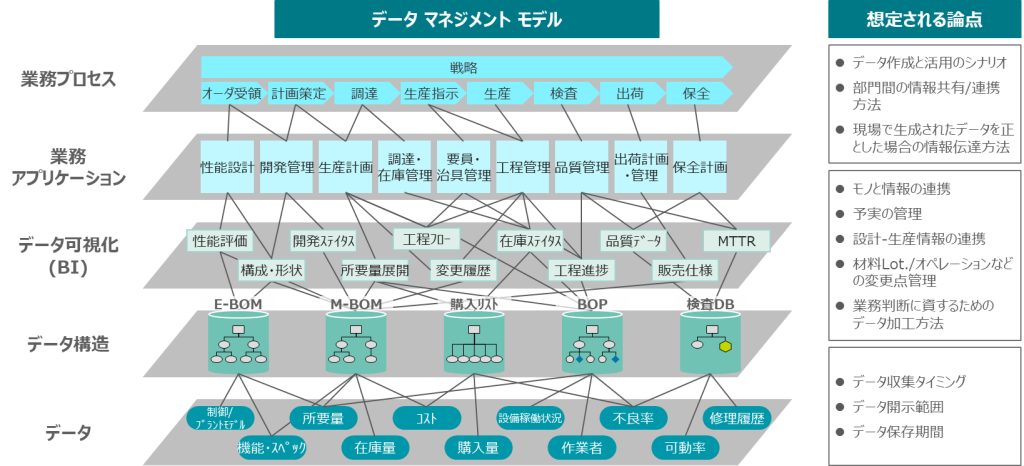
5 慮る力
日本の強み、デジタルで増幅
かつて日本の製造業が世界をリードしていた時代、その競争力の源泉は何だったのか。高精度な部品製造と精密な組み立てを可能にする卓越した技術力は確かに重要な要素だった。しかし、それ以上に重要だったのは、ものづくりにおける複合的な思考・判断ができる「慮る力」ではないだろうか。
この「慮る力」とは、単なる問題解決能力を超えた、日本のものづくりの真髄とも言える能力だ。データや経験から意味のある根拠を抽出し、それを体系化する「根拠構築力」。構築された根拠の重要度を適切に評価し、定量的データと定性的な経験則を組み合わせる「総合的判断力」。要求内容や過去の経緯を踏まえた「文脈理解力」。品質、コスト、納期への影響を総合的に検討する「多角的検討力」。そして、将来起こりうる問題を先回りして考える「予見的思考力」。これらが一体となって、長年にわたり日本の製造業の強みとなってきた。
特筆すべきは、この「慮る力」が、単なる経験則の集積ではなく、暗黙知を形式知として整理し、複数の根拠間の相互関係を考慮しながら体系化された判断基準となっている点だ。これは、単純なデータ分析や論理的思考では代替できない高度な能力である。
ここで注目したいのは、この「慮る力」はデジタル技術と組み合わせることで、さらに強化できるという点だ。例えば、生成AIの登場により、情報の探索や推論プロセスの多くは委ねることが可能になった。これにより、人間は根拠の生成や、その根拠に基づく本質的な判断により多くの時間を費やすことができる。
また、デジタル技術の活用により、より広範な情報やデータを考慮した意思決定が可能になる。例えば、製造プロセス全体への影響、関連部署や協力会社への波及効果、さらには技能伝承や環境負荷など、長期的な持続可能性までを含めた総合的な判断を、より効果的に行うことができるようになる。
つまり、日本の製造業に求められているのは、「慮る力」を捨て去ることではない。むしろ、この強みをデジタル技術でいかに増幅できるかが、これからの製造業の浮沈を左右する鍵となるだろう。
本連載では、DXではなくXDの重要性、そして業務プロセス改革と情報連携の在り方について論じてきた。その集大成として最も強調したいのは、日本の製造業の真の競争力強化は、デジタル技術への置き換えではなく、人間の「慮る力」とデジタル技術との最適な組み合わせにあるという点だ。
その実現には、確かに時間と労力を要する。しかし、これこそが日本の製造業が目指すべき方向性ではないだろうか。デジタル化の波に押し流されるのではなく、日本の強みを活かしながら、新しい時代のものづくりの形を創造していく。それが、製造業に携わる私たちに課せられた使命なのである。
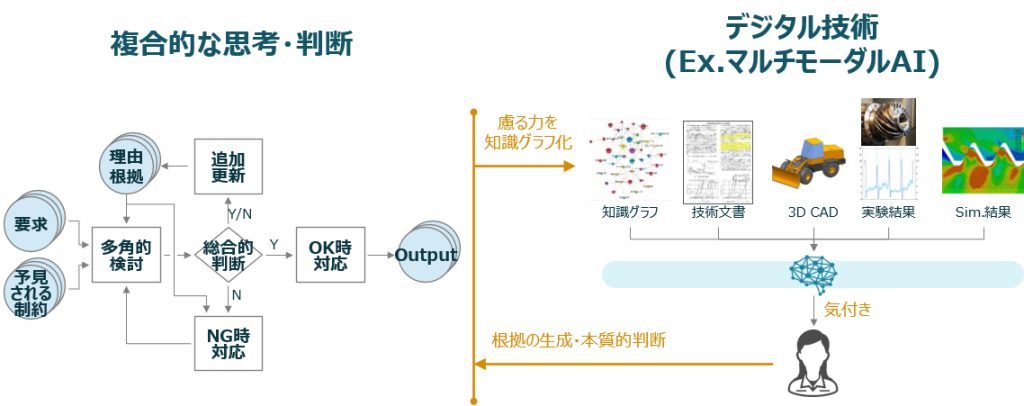